智能貨架客戶案例——制造業(yè)產(chǎn)線邊
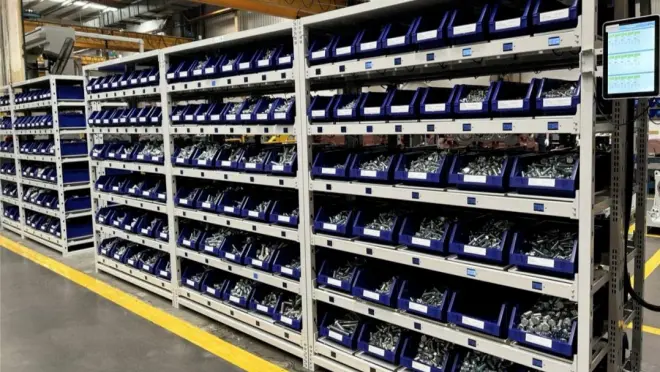
案例背景
客戶背景:該公司是一家跨國知名工業(yè)自動化解決方案提供商,在全球范圍內(nèi)擁有廣泛的業(yè)務(wù)和客戶群體,規(guī)模龐大,設(shè)有多個生產(chǎn)基地、研發(fā)中心和銷售辦事處。該公司在多個國家設(shè)有生產(chǎn)工廠,以滿足不同地區(qū)客戶的需求,為各行各業(yè)的客戶提供服務(wù)。該公司一直致力于實現(xiàn)生產(chǎn)線的高效、可靠和智能化,推動工業(yè)自動化。
客戶訴求:該公司制造規(guī)模龐大,涵蓋了多個產(chǎn)品領(lǐng)域。工廠使用的零部件物料種類高達2000種,消耗量非常大,但仍然采用傳統(tǒng)管理模式,導(dǎo)致生產(chǎn)線邊的零部件物料管理問題越來越大。因此,該公司急于解決這個問題,決定引入智能貨架系統(tǒng)來優(yōu)化其制造業(yè)生產(chǎn)線,從而可以降低成本,并實現(xiàn)覆蓋整個制造工廠的智能化。
解決方案
在這種情況下,磐石電氣的銷售和技術(shù)人員首先分析了該公司制造產(chǎn)線邊物料管理的問題。他們發(fā)現(xiàn),產(chǎn)線上的工人通常直接從傳統(tǒng)貨架上取用零部件物料,在傳統(tǒng)人工管理下,物料的補充和分發(fā)依賴于人工判斷和操作,容易造成物料短缺或供應(yīng)延誤,影響生產(chǎn)進程與生產(chǎn)線不平衡,降低整體生產(chǎn)效率。且傳統(tǒng)方式下,設(shè)備故障往往需要等到發(fā)生后才能得知,故障響應(yīng)不及時,造成制造業(yè)生產(chǎn)線停機時間較長,影響生產(chǎn)計劃。
由于該公司的產(chǎn)線邊物料管理采用的是“自采自用”的方式,并且有自己的軟件管理系統(tǒng),因此磐石電氣為該企業(yè)設(shè)計了適合制造業(yè)產(chǎn)線邊指定區(qū)域放置的智能貨架。每個智能貨架都配備傳感器,通過傳感器和物聯(lián)網(wǎng)技術(shù)實時監(jiān)測貨架上的物料數(shù)量和狀態(tài)。當物料達到預(yù)定的最低庫存水平時,系統(tǒng)會自動發(fā)出補貨請求,減少了工人的物料獲取時間,優(yōu)化了物料管理。
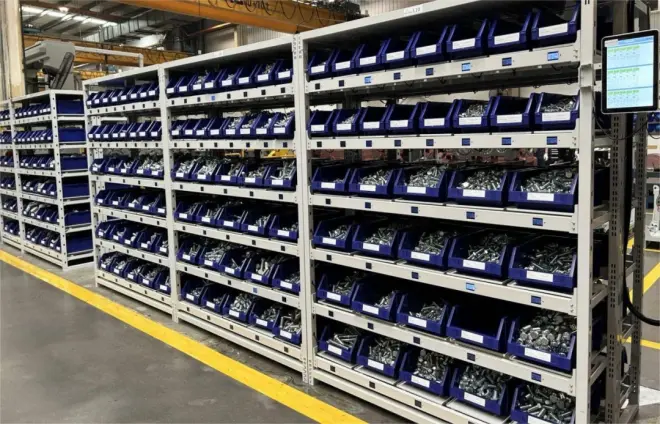
價值實現(xiàn)
1.生產(chǎn)效率提升:減少了物料獲取時間,優(yōu)化了生產(chǎn)線平衡,提高了整體生產(chǎn)效率。
2.成本降低:減少了人力資源浪費,降低了庫存成本和生產(chǎn)停機造成的損失。
3.質(zhì)量提高:更精準的物料供應(yīng)和生產(chǎn)線平衡有助于提高產(chǎn)品質(zhì)量和一致性。
4.數(shù)據(jù)驅(qū)動決策:實時監(jiān)控和數(shù)據(jù)分析使管理層能夠更好地了解生產(chǎn)線狀況,做出及時決策,推動持續(xù)優(yōu)化。