Computational Challenges of AM in Metals, Polymers ,Concrete
Brief CV:
Prof. Miguel Cervera is Civil Engineer (Technical University of Catalonia, UPC, 1983), Doctor of Philosophy in Civil Engineering (University of Wales, 1986), Doctor in Civil Engineering (UPC, 1988).
He is Professor of Continuum Mechanics and Structural Analysis at the School of Civil and Environmental Engineering of Barcelona, Spain. Currently, he is Head of Doctoral Studies and Director of the Structural Mechanics Division.
Prof. Miguel Cervera has published 14 books in Mechanics of Materials and in Structural Mechanics; they are used as reference textbooks in more than 60 under-graduate and post-graduate courses in Engineering and Architecture. Prof. Miguel Cervera has published 139 research papers in JCR scientific journals in the field of non-linear computational mechanics of solids, with focus on finite element technology, non-linear constitutive modeling, and thermo-mechanical and coupled problems and numerical simulation of manufacturing, production and construction processes.
Prof. Miguel Cervera has participated in 70 national and international research conferences, acting in 54 of them as member of the Scientific or the Organizing Committee. He has also co-organized numerous invited sessions and mini-symposiums and has been keynote lecturer in several international conferences. He is member of the Editorial Boards of “Engineering Failure Analysis”, “Metals”, Section for 'Additive Manufacturing', “Metals”, Section for 'Welding and Joining', “Metals”, Section for 'Metal Casting, Forming and Heat Treatment', “Frontiers in Built Environment”, Section for ‘Computational Methods in Structural Engineering’.
Prof. Miguel Cervera has participated in several European and Spanish competitive research projects, related to the application of the finite element method to the development of tools for Computer Aided Engineering, with focus on industrial manufacturing processes with thermal, metallurgical and chemical interactions. He participates in the High-End Expert Program with Tongji University, Shanghai, China funded by the Chinese Science Council.
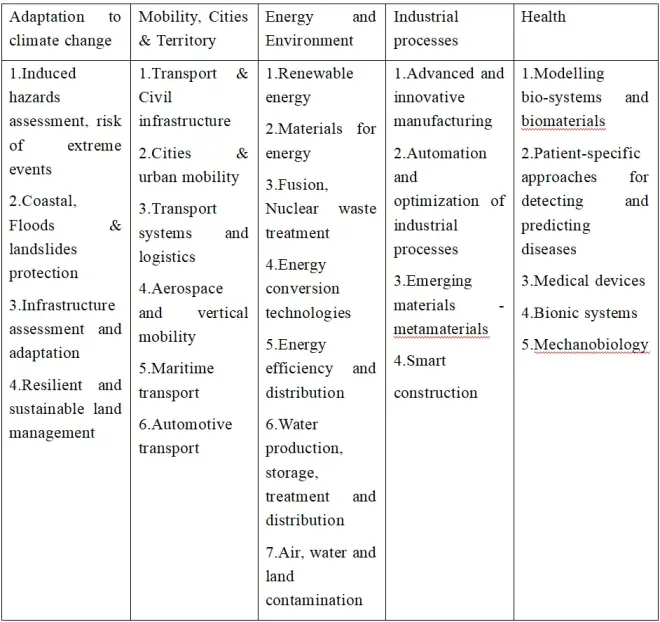
Outline
Introduction
? ? AM technologies for metals:
? ? Available technologies
? ? Processing: Computational framework
AM technologies for polymers:
? ? Available technologies
? ? Performance: Computational strategy
AM technologies for concrete:
? ? Available technologies
? ? Buildability: Computational framework
? ? Concluding remarks and Acknowledgments
Introduction
Additive Manufacturing (AM) is being widely and rapidly adopted for fabrication of products and components in many industrial sectors: aero, locomotive, biomedical, construction, etc.
AM main advantages are freedom of design, customization and automation at levels unattainable for classical manufacturing procedures.
AM is an active area of innovation in metallic, polymeric and cement-based materials. For each application, AM poses open questions related to material science, structural design, construction and manufacturing techniques, reliability and sustainability.
Among these some of the main aspects to be considered are: the effects of the manufacturing processing parameters, the assessment of the performance of the fabricated components and the buildability of the designs.
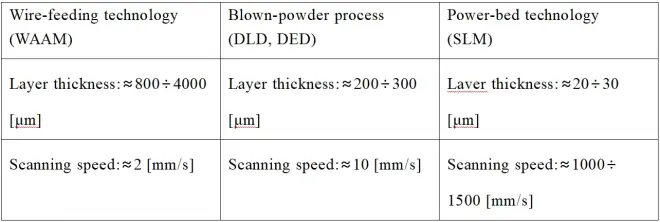
Processing:Computational framework
Wire-feeding technology (WAAM, DED)
? ? Coupled thermo-mechanical analysis
? ? Moving heat source following the actual scanning pattern:
? ? g-code format
? ? ? Highly accurate?solution of both temperature and stress fields
Power-bed technology (SLM)
? ? Stress analysis by inherent strains method
? ? Layer-by-layer or lumped multi-layers activation strategies
? ? ? Approximate solution: only distortions for dimensional control
Why high-fidelity analysis?
The numerical model reproduces the actual industrial AM process, as closely as possible, including:
?The actual scanning strategy, recoating time and cooling periods.
?The actual process parameters: power imput, scanning speed, beam size, metal feeding
This allows high-fidelity:
?Microstructure modelling: temperature and cooling rate drive metallurgical evolution
?Stress analysis: temperature and temperature gradient drives deformation and plasticity
Computational framework
?FE method
? Both conformal and not conformal meshing can be used
? Fix mesh or automatic refinement/coarsening (octree based) strategies
?Building process
? Born-dead elements technique: only active elements are computed and assembled into the?global system of equations representing the actual computational domain
? Octree-based searching algorithm
?Multi-physics analysis
? Coupled thermo-mechanical framework (implicit)
? Coupled with the microstructure analysis (JMAK)
?Non-linear analysis
? Newton-Raphson, quasi-Newton, etc.
? Line-search algorithm
? Predictor-corrector
Stress analysis
?Constitutive laws
Solid?phase: visco-elastic J2-visco-plastic constitutive law
Strain-hardening is mandatory
Annealing is important (annealing temperature is usually much lower than the melting temperature)
Mushy and liquid phases: purely visco-plastic (isotropic) behaviour
Temperature-dependent material properties (thermal softening)
Thermal deformations + shrinkage due to liquid-to-solid transformation drive the thermal stresses
?FE technology
FE technology able to deal with isochoric behaviour is required
Hexahedral meshes: QIPO or B-bar elements
Tetrahedral meshes: mixed-UP formulations (GLS, OSS, mini-element)
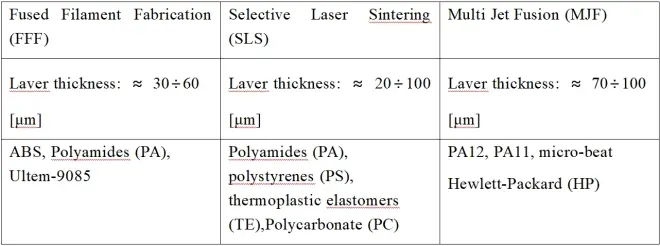
Performance:Computational strategy
??Not only Rapid Prototyping... but Structural components
??In-service analysis and performance of 3D-printed component
??Optimization of printing parameters
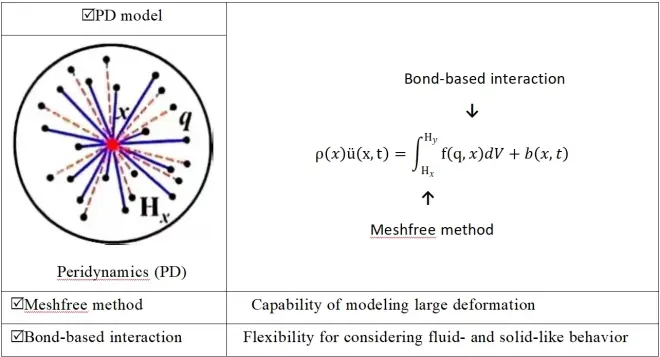
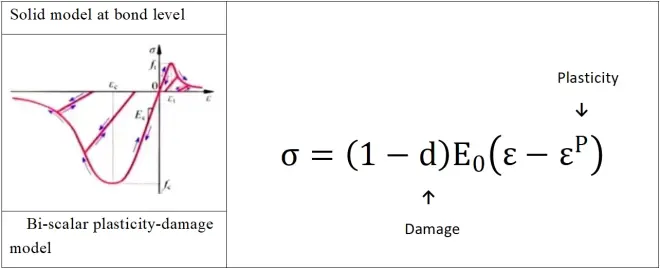
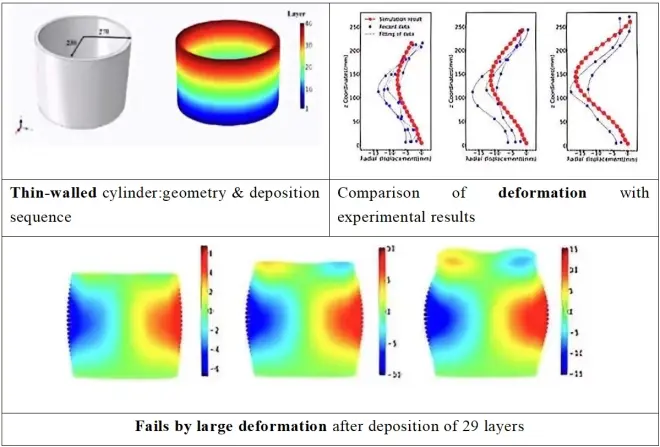
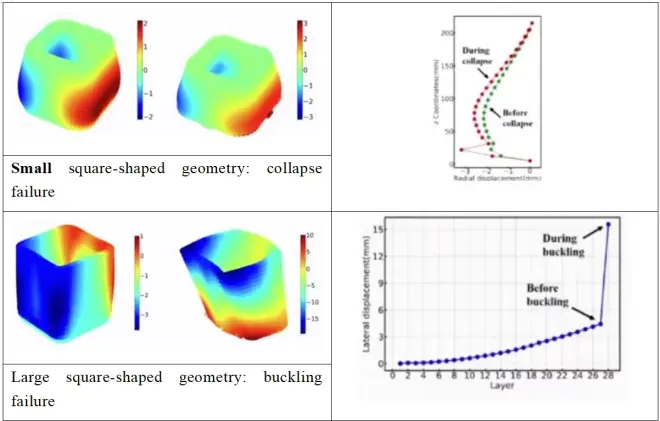
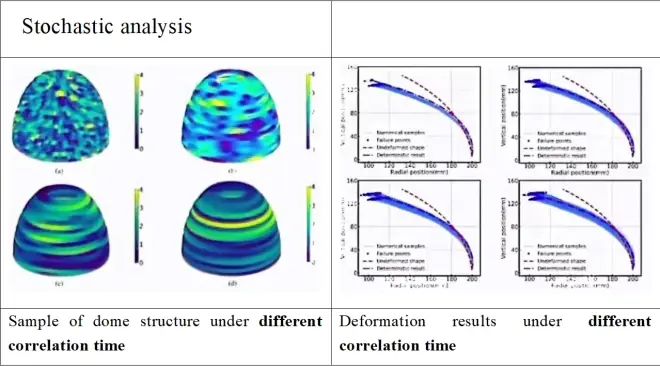
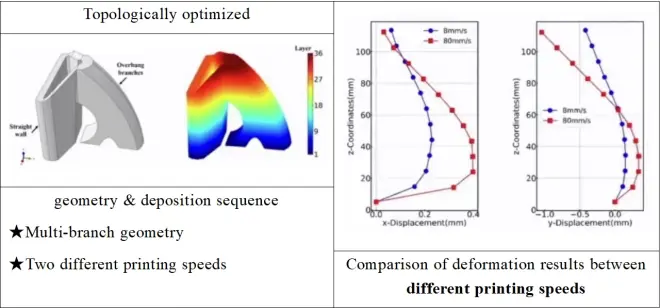
?In this talk, the experience of the International Center of Numerical Methods in Engineering (CIMNE) in the computational modelling of AM is reviewed.
?Three main topics are addressed: the processing of metal components at industrial scale, the assessment of the mechanical performance of polymeric products and the buildability of 3D printed concrete structures.
?Remarkable accuracy in the simulation of AM processes using different technologies and materials (metals, polymers and concrete) has been achieved.
?..there is still a lot to do !