豪普鈦業(yè)鈦白粉白段新工人入廠簡明培訓(xùn)教材(2004年版)
豪普包膜段[白段]新工人入廠簡明培訓(xùn)教材(2004年版)
一、?產(chǎn)品概況
鈦白粉(學(xué)名二氧化鈦, TiO2), 具有很好的化學(xué)穩(wěn)定性、耐候性、著色力、遮蓋力及白度,是世界上性能最佳、應(yīng)用最廣、用量最大的白色無機顏料。全球年市場值達(dá)70億美元,已成為世界無機化工產(chǎn)品中三種最大銷售值商品之一,僅次于合成氨和磷酸,名列第三位。按TiO2晶型結(jié)構(gòu),鈦白粉可分為銳鈦型和金紅石型兩類。金紅石型鈦白粉晶型穩(wěn)定、結(jié)構(gòu)致密,物化及光學(xué)性能指標(biāo)優(yōu)于銳鈦型鈦白粉,因而用途更廣、產(chǎn)量更大。
二、?鈦白粉的物理性質(zhì)
二氧化鈦是一種白色粉末,在自然界中有三種結(jié)晶形態(tài):板鈦型、銳鈦型和金紅石型;分別相當(dāng)于三種氧化物礦:板鈦礦、銳鈦礦和金紅石礦。但工業(yè)制品只有銳鈦型(A型)和金紅石型(R型)兩種,這兩種晶形都屬于四方晶系,金紅石是細(xì)長的成對的孿生晶體,每個晶胞含有兩個TiO2分子,以兩個棱邊相連;而銳鈦型則以八面體的形式出現(xiàn),氧原子位于八面體的頂角,每個銳鈦晶胞含有四個TiO2分子,以八個棱邊相接。在這三種晶型中,板鈦晶體最不穩(wěn)定,加溫至650℃時即直接轉(zhuǎn)化為金紅石晶體。銳鈦晶體較為穩(wěn)定,但在高溫下也要轉(zhuǎn)化為金紅石晶體。金紅石晶體最穩(wěn)定,它不會再轉(zhuǎn)化,晶體結(jié)構(gòu)也最致密。因此,它的硬度、比重、介電常數(shù),折光指數(shù)等也最高,表一是這些晶體的一些物理常數(shù)。
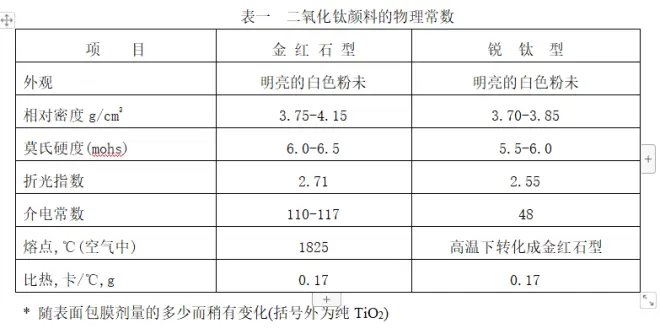
三、?鈦白粉的化學(xué)性質(zhì)
二氧化鈦是鈦最重要的化合物,分子式為TiO2分子量79.9,它無毒,是一種化學(xué)性質(zhì)十分穩(wěn)定的(偏酸性)氧化物。在常溫下,幾乎不與其他化合物(包括元素)作用。不溶于水、稀酸、脂肪酸、有機酸和弱無機;大氣中的二氧化碳、氮、硫化氫、二氧化硫、氨、氧等氣體對它也不起作用。微溶于堿和熱硝酸。只有在長時間煮沸的條件下,才能完全溶于濃硫酸和氫氟酸。若沒有還愿劑存在,即使在1800℃的高溫下也不與氯氣作用。二氧化鈦這種化學(xué)穩(wěn)定性,完全由其晶體特性所決定。在二氧化鈦晶體結(jié)構(gòu)中,一個鈦粒子被六個氧粒子所包圍,而四價鈦粒子與二價氧粒子之間又有很強的結(jié)合力。然而,在某些特定條件下,二氧化鈦也會發(fā)生脫氧反應(yīng),生成鈦酸鹽或鈦的其他化合物。
????二氧化鈦不溶于水、對酸的作用是很弱,只有在高溫和長時間煮沸下,才溶于氫氟酸和濃硫酸。
??
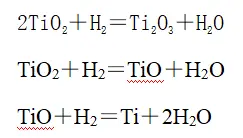
其溶解速度常和生產(chǎn)二氧化鈦的煅燒溫度有關(guān),一般煅燒溫度越高,則溶解速度越慢。為了加速溶解,可在硫酸中加入硫銨、堿金屬硫酸鹽或過氧化氫。二氧化鈦與酸式硫酸鹽(如硫酸氫鉀)或焦硫酸鹽(如焦硫酸鉀)共溶,即轉(zhuǎn)變可溶性硫酸氧鈦。
????????TiO2+2KHSO4=TiOSO4+K2SO4+H2O????二氧化鈦能微溶于堿,與強堿(氫氧化鉀)或堿金屬碳酸鹽(碳酸鈉、碳酸鉀)熔融,則轉(zhuǎn)化為可溶于酸的鈦酸鹽。
????????TiO2+4NaOH=NaTiO4+2H2O
以上兩種方法,在化學(xué)分析方法中被廣泛應(yīng)用。????在高溫下,如有還原劑(如碳)存在,二氧化鈦能被氯氣氯化生成四氯化鈦。
????????TiO2+2C+2Cl2=TiCl4+2CO
????如沒有還原劑則不發(fā)生反應(yīng)。這就是氯化法生產(chǎn)中鈦礦氯化時發(fā)生的反應(yīng)。二氧化鈦在高溫下可被氫、鈉、鎂、鋁、鋅、鈣及某些變價元素的化合物還原成低價鈦的化合物,但很難還原成金屬鈦。如將干燥的氫氣通入赤熱的二氧化鈦,可得到Ti2O3;在2000℃、150大氣壓的氫氣中,也只能獲得TiO,但是若將金紅石型二氧化鈦噴入等粒子室中,呈細(xì)液滴狀的二氧化鈦與氫氣等粒子遺流接觸,則可被還原成鈦和水蒸氣。????????2TiO2+H2=Ti2O3+H2O
????????TiO2+H2=TiO+H2O????????TiO+H2=Ti+2H2O????若在溶融氯化鈣中電解二氧化鈦,或在高于鈦的熔點溫度下,將二氧化鈦溶解在氟化鈣中,可制備金屬鈦。若用CaH2還原二氧化鈦得到TiH4,如進(jìn)一步脫氫,則可以得到粉末鈦。????二氧化鈦與金屬鈉反應(yīng),可生成Ti2O3、TiO和鈦酸鈉。在不同的條件下,二氧化鈦與碳作用,分別生成Ti2O3和TiC。????總之,二氧化鈦的化學(xué)性質(zhì)非常穩(wěn)定,只有在一些特定條件下,才能發(fā)生某些反應(yīng)。
四、?鈦白粉的顏料性能
所謂顏料特性,主要是指顏色、遮蓋力、著色力、耐候性和吸油量等指標(biāo)。
????1.顏色
????作為一種白色顏料,這里指的是它的白度。
????我們知道,白晝的自然光(日光)是由許多不同的波長的光波組成。每一種波長的光具有它特定的一種顏色。各種不同顏色的光組合起來,就成為白光。而物體的不同顏色是由于它們對自然光中不同波長的光波吸收或反射的程度不同而產(chǎn)生的。二氧化鈦能對各種不同波長的光均勻地反射,因而呈現(xiàn)白色。
????但TiO2與可見光的作用并非完美無缺,它在均勻反射的同時,對可見光近紫外的400-500nm區(qū)域具有一定的吸收作用,因而和最佳的白色顏料氧化鎂比帶有輕微的乳黃色,而銳鈦型的吸收程度比金紅石型小,所以比金紅石型外觀銷呈藍(lán)相。在硫酸生產(chǎn)中,影響鈦白粉白度的主要因素,首先是它所含有的有害雜質(zhì)的種類和含量。對某些雜質(zhì),即使含量甚微,也會對白度產(chǎn)生明顯的影響。這類雜質(zhì)主要有鐵、鉻、鈷、鈰、銅、錳、釩、鉛等。以鐵為例,對銳鈦型而言,當(dāng)Fe2O3含量達(dá)到0.009%時,即會呈現(xiàn)黃色。同時,這也與鈦白的晶型有關(guān),一般地說,金紅石型對雜質(zhì)更為敏感,當(dāng)Fe2O3含量達(dá)到0.003%時即會顯示色彩。而氯化法TiO2的生產(chǎn)中,由于所用的原料TiCl4已經(jīng)過仔細(xì)蒸餾凈化,所以其產(chǎn)品的白度有可能會更好一些。
????其次,是鈦白顆粒的形狀、大小和粒度分布。其形狀要求外型輪廓光滑,不帶棱角,因為帶棱角的表面會減弱對光的反射。對粒子大小,一般地說是越細(xì)越好,但也不能太細(xì),最理想的粒徑為0.2-0.4微米,從理論上說就是相當(dāng)于可見光的半波波長,當(dāng)小于此值時粒子將會成為透明的。對于粒度分布,則要求均勻,分布帶要窄。
白度通常是以顏色指數(shù)(Color index,簡稱CI)表達(dá)的。通過測定TiO2顏料在紅(R),綠(G),藍(lán)(B)光下的反射值,按下式進(jìn)行計算:
顏色指數(shù) ??CI=(R-B)/G×100
計算后如為正值,表示顏料呈黃相;負(fù)值表示呈藍(lán)相。
2、光澤
光澤是人們?nèi)庋蹖ξ矬w表面所反射的光線強度的感覺,是一種觀察者的主觀效應(yīng)。
光澤是表層涂料(面漆)的一項重要指標(biāo),涂層中TiO2顏料的分布和濃度對光澤有重要的影響。如果涂膜表面光滑平整,則能折射出鏡面般的光澤,然而,由于含有顏料以及流平性不佳等原因,涂膜總是存在一定的粗糙度。
涂膜中應(yīng)用TiO2顏料的主要原因是利用其不透明度和白度。但如果用量增加,涂膜的表面粗糙度上升,光線在涂膜表面不單是反射,而且會產(chǎn)生散射或漫射現(xiàn)象,所以涂膜的光澤就會下降。因為涂膜的平整度很大程度上受顏料分散度的影響,所以提高顏料的分散性對其在大多數(shù)體系中的應(yīng)用都是相當(dāng)重要的。當(dāng)然,應(yīng)用體系中如含有絮凝劑對光澤也是不利的,因為它會使顏料粒子絮凝,導(dǎo)致涂膜表面不平整。
3、著色力和消色力
????顏料的著色力是指當(dāng)它加入到一種涂料介質(zhì)中以后能改變該種涂料色彩,并呈現(xiàn)出自身色彩的能力。著色力的更新替代名稱是消色力,它是指TiO2在一種涂料中能消除該種涂料色彩,呈現(xiàn)出自身色彩的能力。我國TiO2現(xiàn)行國標(biāo)中規(guī)定:是在特制的含有群青的藍(lán)色漿料中,加入定量的TiO2制成的漿料,再與用標(biāo)準(zhǔn)TiO2樣品制成的漿料進(jìn)行色彩比較,稱為相對消色力。對白色顏料而言,消色力不只是由這種白色顏料本身的性質(zhì)而定,還取決于體系的所有組分,包括黑色或有色顏料和載色劑,以及它們之間的相互作用。
????二氧化鈦消色力的大小直接取決于它對可見光的散射能力,散射系數(shù)越大,則消色力也越大。一般說來,有較高的折射率,就有較高的消色力。消色力還隨著粒度的減小和粒度均勻性的增加而增大。金紅石型鈦白之所以在白色顏料里消色力最高,就是因為它的折射率最大、粒度小而均勻(在0.15-0.3微米)。
????二氧化鈦的消色力還與它的制備條件有關(guān)。例如:提高鈦液的穩(wěn)定性、確定合適的鐵鈦比和酸比值(F值),優(yōu)化晶種和水解的方法和條件,配以正確的煅燒和粉碎的操作,對提高消色力乃至遮蓋——最重要的顏料性能是至關(guān)重要的。
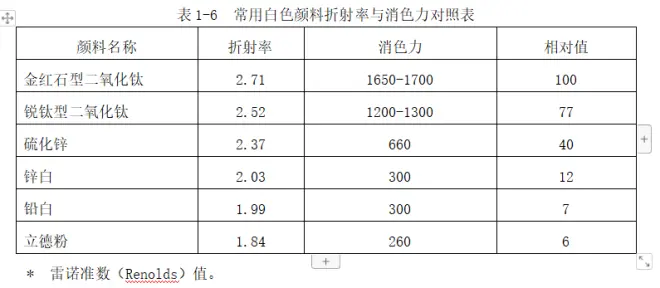
????4、耐候性(耐久性)
????耐候性是指顏料在日光曝曬下,能抵抗大氣的作用。避免發(fā)生黃變、失光和粉化的能力。影響涂膜的耐久性歸結(jié)于兩方面的原因:樹脂基料由于紫外線的作用出現(xiàn)降解;TiO2顏料的光化活性。
TiO2顏料的光化活性是因吸收紫外線而引起的。TiO2對涂膜降解究竟是起促進(jìn)或延緩作用,取決于其光化活性是大于或小于樹脂基料單獨存在時被降解的速度。TiO2光化活性引起涂膜降解的機理是:吸收了紫外線之后,激發(fā)出電子,在晶格中留下帶正電性的空穴,這種激發(fā)電子和空穴可能在晶格內(nèi)重新結(jié)合,也可能游離到晶格表面,于是,便發(fā)生引起周圍基料介質(zhì)一連續(xù)的化學(xué)反應(yīng):
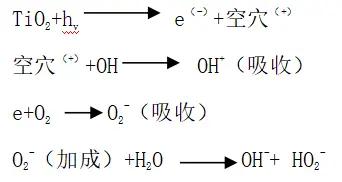
反應(yīng)中所產(chǎn)生的羥基和過羥基團都能引發(fā)有機樹脂基料分子的破壞。從反應(yīng)式中很明顯看出,氧氣和濕氣是TiO2發(fā)生光催化降解現(xiàn)象的基本條件。
在TiO2的兩種晶型的產(chǎn)品中,銳鈦型的光化活性要大于金紅石型。
為了降低TiO2,尤其是用于戶外金紅石型TiO2的光化活性,提高其耐久性,可以考慮的途徑有兩種:首先是在金紅石型的晶格中混入能起穩(wěn)定作用的元素(一般為鋅和鋁),使晶格中的空穴和電子的位置固定,防止其到達(dá)晶粒表面,另外用致密的硅、鋁的氧化物,更新的是用鋯的水合氧化物對金紅石型晶?;w進(jìn)行包覆,在TiO2晶粒表面形成屏障,避免出現(xiàn)降解現(xiàn)象。這兩種技術(shù)的綜合應(yīng)用,能很大程度上降低TiO2的光化學(xué)活性,從而又開發(fā)出一系列的高耐久性的產(chǎn)品。
????5、吸油量
????顏料的吸油量是指每100g顏料在達(dá)到完全潤濕時所需要用油的最低克數(shù),用百分率表示。
????吸油量是產(chǎn)品粒徑、粒形、比表面積和粒子表面狀態(tài)的函數(shù),也是顏料的三大關(guān)鍵指標(biāo)(消色力、顏色、吸油量)之一。對吸油量應(yīng)有正確的認(rèn)識,并不能簡單地認(rèn)為總是越低越好。對用于溶劑型涂料、塑料等領(lǐng)域的顏料,吸油量應(yīng)盡可能低,因為高吸油的顏料在這些產(chǎn)品中應(yīng)用會造成多費基料及引起涂料產(chǎn)品粘度增稠等弊端。但是對于平光乳膠漆,為了使在高PVC下的涂膜產(chǎn)生高的干遮蓋力,所應(yīng)用的TiO2顏料必須經(jīng)過高量疏松狀無機表面包膜(SiO2/Al2O3),這種包覆物是多孔性的,比表面積大,因而吸油量也大。如R-780的吸油量為33,而R-780-2為40以上。
????6、光色互變現(xiàn)象
含有氧化鐵、氧化鉻、氧化鎳等雜質(zhì)的二氧化鈦在陽光照射下會變?yōu)楹稚?,離開陽光后恢復(fù)原色,這一性質(zhì)稱為光色互變現(xiàn)象,但純二氧化鈦一般無此性質(zhì)。
?
五、?產(chǎn)品的用途
由于TiO2有十分卓越的物理、化學(xué)、光學(xué)和顏料性能,因此被廣泛應(yīng)用于涂料、塑料、造紙、橡膠、油墨、化學(xué)纖維、電容器、搪瓷、食品、化妝品等工業(yè)。近年來,國外在大力開發(fā)它的新應(yīng)用領(lǐng)域,如催化劑(或催化劑載體),二氧化鈦溶膠無機粘合劑、吸附劑、紫外線吸收劑、鈦纖維、納米二氧化鈦、光催化劑二氧化鈦等。鈦白粉有如此眾多與國民經(jīng)濟的發(fā)展息息相關(guān)的用途,因此鈦白粉消費量的多寡,可以衡量一個國家人民生活水平的高低。
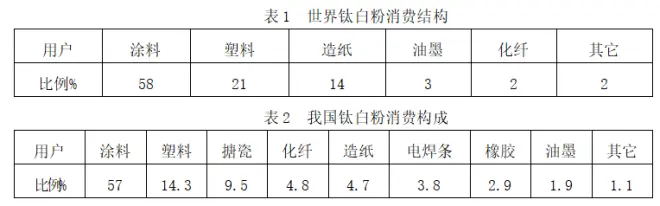
從世界范圍來說,TiO2顏料的最主要應(yīng)用領(lǐng)域是涂料、塑料、紙張,這三個領(lǐng)域所消費的TiO2占全球TiO2總消費量的比例分別為58-60%、18-20%和13-14%,其余領(lǐng)域的消費量只占8-10%。
????現(xiàn)將TiO2顏料在一些主要部門中的應(yīng)用簡介如下:
涂料
TiO2顏料是涂料工業(yè)中用量最大的一種顏料,在涂料工業(yè)中的消費量占涂料工業(yè)中的消費各種顏料總量的90%,據(jù)權(quán)威性統(tǒng)計資料,全球涂料工業(yè)所消費的TiO2占TiO2顏料總消費量的58-60%。我國的此項消費比例更高一些,約為60-65%左右。據(jù)有關(guān)統(tǒng)計資料,涂料工業(yè)消費的TiO2中,99%是金紅石型,其中77%為中低TiO2含量的R2型,22%是含高處理劑和低TiO2含量的R3型銳鈦型只占消費量的1%。
特別是作室外的白漆、色漆和各種樹脂漆、乳膠漆必需的原料,以鈦白為白色顏料生產(chǎn)的油漆和油墨具有色彩鮮艷、壽命長等優(yōu)點。
造紙工業(yè)
從世界范圍來說,紙張是TiO2顏料的第三大用戶,但在美國,紙張行業(yè)用TiO2的比例超過塑料,居第二位。
紙張中添加TiO2顏料的目的主要是賦予不透明度和白度,其次是改進(jìn)的平滑度和機械性能,提高光澤和可印刷性能。除TiO2外,紙張工業(yè)中常用的填充料有滑石粉、碳酸鈣、硫酸鋇等。
紙張工業(yè)中使用的TiO2有兩種方式,一是與其它填料一起直接加入到紙漿中。經(jīng)過制漿、壓濾、烘干,成為紙張的一種組分。另一種是涂布在紙張在紙張表層制成裝飾性的涂布紙。
紙張用TiO2應(yīng)以銳鈦型為主,因為它具有色調(diào)明顯的偏藍(lán)底相,使紙張外觀更為潔白,戶外用紙張制品中應(yīng)使用細(xì)粒徑的金紅石型產(chǎn)品。
紙張工業(yè)用的TiO2,主要品質(zhì)要求是細(xì)粒徑,具有高度的水分散性,良好的遮蓋力以及與紙張纖維的結(jié)合率(留得率),雜質(zhì)含量少,白度高,銳鈦型一般不需經(jīng)過表面處理。
紙張用TiO2有兩種產(chǎn)品形式,一是紙袋裝粉料,使用時連同包裝袋,一起投入化漿槽中;另一種是水性漿料。兩種形式產(chǎn)品各具特色,前者運輸方便,后者有利于紙張質(zhì)量,且省去了生產(chǎn)中的干燥和粉碎工序,是美國造紙工業(yè)用TiO2的主要產(chǎn)品形式。
塑料工業(yè)
????塑料是TiO2顏料的第二大用戶,占世界TiO2總需求量的18-20%。TiO2在塑料中的加入量隨著塑料品種和塑料制品的應(yīng)用場合而異,一般在0.5-5%之間。
TiO2的不透明性大、白度高、化學(xué)穩(wěn)定性好、與合成樹脂、催化劑、增塑劑等接觸不起反應(yīng),是制造白色或彩色塑料最優(yōu)良的不透明劑、著色劑和填充劑。加有鈦白的塑料不僅可提高強度,呈藍(lán)色底相,延長壽命,不影響其絕緣性能、抗張力和伸長率,而且用量省、色彩鮮艷、無毒。
另外,由于TiO2顏料必須具有良好的耐熱性能,以及高分散性。所以用于塑料的TiO2,一般都經(jīng)過無機包膜處理,但處理量均不大,含量較高。與涂料系統(tǒng)一樣,戶外塑料TiO2用必須應(yīng)用金紅石型,其它可以用銳鈦型。
橡膠工業(yè)
????鈦白在橡膠工業(yè)中,除作為著色劑,尚有補強、防老、填充作用,用鈦白制的得的白色和彩色橡膠制品在日光照射下耐曝曬、不龜裂、不變色、老化慢、強度高、伸展率大,并具有耐酸和堿的性能。在硅橡膠中加入鈦白,可提高橡膠的耐熱性和穩(wěn)定性。
化纖工業(yè)
????二氧化鈦是一種優(yōu)良的消光劑,常被用來進(jìn)行消光與內(nèi)消光,在紡絲的原液中加0.2-3.0%的鈦白,就能得到很好的永久性消光和崐增光效果,而不影響纖維的強度和物理性能,還能提高韌性。用鈦白效果的化纖產(chǎn)品,易染色、手感好,耐穿用。
搪瓷
????各種常用的搪瓷用品,就是在金屬胚體的表面涂抹一層瓷釉,經(jīng)高溫熔合而成,能起到保護及美觀作用。
????瓷釉又稱琺瑯,常用的有銻琺瑯和鈦琺瑯兩種,與銻琺瑯相比,鈦琺瑯的特點是:由于鈦白折射率高,鈦的乳濁度和遮蓋力也高,因而可以涂得很薄,使制品的重量輕,并能提高瓷層的耐壓、耐彎、耐沖擊等機械強度。
?電焊條
????二氧化鈦是電焊條外層藥皮的主要成分,它的主要作用是穩(wěn)定電弧不使發(fā)生爆濺,同時由于這種熔渣的熔點較低,使熔渣的粘度降低,從而降低焊條上金屬熔滴的表面張力,使焊條結(jié)構(gòu)更為緊密。其次,熔渣覆蓋在焊接點表面,可以形成保護膜,隔絕空氣,防止了金屬的高溫氧化,而且,它還能使焊縫容易脫渣。
其他
????除了上述用途外,鈦白還廣泛用于冶金、電子陶瓷等領(lǐng)域,在香皂、香粉、香脂、牙膏等化妝品中用作白色填料,它可以用來制造含鈦白的特種玻璃,在皮革和制藥工業(yè)中用作著色劑……
?
六、?產(chǎn)品的生產(chǎn)方法和工藝流程
(一)?產(chǎn)品的生產(chǎn)方法
鈦白的生產(chǎn)方法有硫酸法和氯化法。
(二)?產(chǎn)品生產(chǎn)的工藝流程
1)?硫酸法的工藝流程
硫酸法生產(chǎn)鈦白是成熟的生產(chǎn)方法,這種方法也適用于生產(chǎn)非顏料用鈦白。硫酸法生產(chǎn)鈦白的原料為鈦鐵礦或鈦渣。下面主要敘述以鈦精礦為原料的生產(chǎn)方法。
????1、工藝流程
????硫酸法生產(chǎn)鈦白主要由下列幾個工序組成:原礦準(zhǔn)備;用硫酸分解精礦制取硫酸鈦溶液;溶液凈化除鐵;由硫酸鈦溶液水解析出偏鈦酸;偏鈦酸煅燒制得二氧化鈦以及后處理工序等。
????2、工藝流程簡述
????(1)原礦準(zhǔn)備
????按照酸解的工藝要求,用雷蒙磨磨礦,將鈦精礦粉碎至一定的細(xì)度。
????(2)硫酸鈦溶液的制備
????鈦液的制備實際上包括鈦精礦的酸分解,固相物的浸取,還原等工藝步驟。
????酸分解作業(yè)是在耐酸瓷磚的酸解罐中進(jìn)行的。將濃度為92-94%的濃硫酸裝入酸解罐中并通入壓縮空氣,在攪拌的情況下加入磨細(xì)的鈦精礦。精礦與硫酸的混合物用蒸氣加熱以誘酸解主反應(yīng)的進(jìn)行,主反應(yīng)結(jié)束后,讓生成的固相物在酸解罐中熟化,使鈦精礦進(jìn)一步分解,分解后所得固相物基本上是由鈦鐵硫酸鹽和一定數(shù)量的硫酸組成。
????固相物冷卻到一定溫度后,用水浸出,并用壓縮空氣攪拌,浸出完全以后,浸出溶液用鐵屑還原,將溶液的硫酸高鐵還原成硫酸亞鐵。
???(3)鈦液的凈化
????鈦液凈化包括沉降、結(jié)晶、分離、過濾等工序。
????沉降是借助于重力作用,向鈦液中加入 ?沉降劑(主要是絮凝劑改性聚丙烯酰胺),除去鈦液中的不溶性雜質(zhì)和膠體顆粒,使鈦液初步凈化。
????冷凍結(jié)晶在冷凍鍋中進(jìn)行,所主要利用硫酸亞鐵的溶解度隨著鈦液溫度降低而降低的性質(zhì)。用冷凍鹽水帶走鈦液熱量,使其降至適當(dāng)?shù)臏囟?,從而使大量的硫酸亞鐵結(jié)晶析出。
????分離、過濾是由錐藍(lán)離心機分離,抽濾及板框壓濾三個工序構(gòu)成。冷凍后的鈦液經(jīng)錐藍(lán)離心機分離及抽濾池抽濾,得到初步凈化的稀鈦液,最后將稀鈦液通過板框壓濾,得到符合生產(chǎn)需要的清鈦液。
????(4)鈦液濃縮
????鈦液濃縮采用連續(xù)式薄膜蒸發(fā)器,在減壓真空的條件下蒸發(fā)掉鈦液中的水份,以符合水解工序的需要。
????(5)水解
????水合二氧化鈦是由鈦的硫酸鹽溶液熱水解而生成的。為了促進(jìn)熱水解反應(yīng),并使得到的水合二氧化鈦符合要求,一般采用引入晶種或自生晶種的方法。
????(6)水洗及漂洗
????由于水解反應(yīng)是在較高的酸度下進(jìn)行的,因此大部分雜質(zhì)磷酸鹽仍以溶解狀態(tài)留在母液中。水洗的任務(wù)是將水合二氧化鈦與母液分離,再用水洗滌以除盡偏鈦酸中所含可溶性雜質(zhì)。經(jīng)過水洗而仍殘留在水合二氧化鈦中的最后一部分雜質(zhì)(高鐵為主),則以漂洗來除去,即在酸性條件下以還原劑將不溶的高鐵還原為可溶性的亞鐵,再進(jìn)行二次水洗。
????(7)鹽處理
????鹽處理是在鹽處理鍋中進(jìn)行。
????在充分?jǐn)嚢璧那闆r下,向偏鈦酸漿液中加入碳酸鉀和磷酸等鹽處理劑,可防止煅燒物料燒結(jié),隱蔽雜質(zhì)元素的顯色,使煅燒產(chǎn)品顆粒松軟,色澤潔白等。
????(8)煅燒
????迥轉(zhuǎn)窯是目前最廣泛采用的煅燒設(shè)備。
????鹽處理后的偏鈦酸在迥轉(zhuǎn)窯中經(jīng)高溫脫水、脫硫及晶型轉(zhuǎn)化等過程,得到具有顏料性能的鈦白粉。
????(9)后處理
????二氧化鈦后處理是按照不同用途對煅燒所得二氧化鈦進(jìn)行各種處理以彌補它的光活性缺陷,并改變它的表面性質(zhì)。后處理包括分級,無機和有機表面包膜處理,過濾,干燥、超微粉碎和計量包裝等,從而獲得表面性質(zhì)好,分散性高的二氧化鈦成品。
????總之,硫酸法的優(yōu)點是可直接用鈦鐵礦作原料,設(shè)備簡單,工藝技術(shù)容易掌握,缺點是三廢量大,不利于環(huán)境保護,并且處理三廢費用很多,從而使生產(chǎn)成本增加。為克服上述缺點,采用含TiO2 70-80%的鈦渣為原料,不但可降低硫酸消耗的三分之一,而且廢副產(chǎn)品物排出量可減少30%。
2)?氯化法的工藝流程
A、氯化
氯化法生產(chǎn)鈦白,首先是制備四氯化鈦(TiCl4)。由于它也是生產(chǎn)鈦金屬的第一步,所以過去一些氯化法鈦白生產(chǎn)商從鈦金屬生產(chǎn)商那里購買一定的TiCl4,特別是新建鈦白廠試生產(chǎn)時。但是鈦白生產(chǎn)商的常規(guī)作法是在現(xiàn)場自己生產(chǎn)TiCl4。
要生產(chǎn)TiCl4,需將鈦原料與燒結(jié)石油焦和預(yù)熱后的氯氣混合在800℃-1000℃的溫度下進(jìn)行反應(yīng)。一些生產(chǎn)商,尤其是美禮聯(lián)和英國的Tioxide,使用冶金焦和石油焦混合物。
反應(yīng)是在流態(tài)化床氯化器中進(jìn)行的,盡管有些生產(chǎn)商使用靜態(tài)床或軸式氯化器。在后者情況下,鈦原料在使用前必須制成團或燒結(jié)。因為未反應(yīng)的物料要在床中堆積,所以靜態(tài)床氯化器必須定期停車清理。而對流態(tài)化床氯化器而言,是將預(yù)定粒度范圍內(nèi)的鈦原料和焦碳直接加至床中。
氯化器通常用鋼制成,襯有耐火材料并罩有外部水冷套。高溫下的氯氣和四氯化鈦極具腐蝕性,所以即便是采用優(yōu)質(zhì)耐火材料,其使用壽命也是相對有限的。
焦中碳的主要目的是將鈦原料脫氧,使所含金屬氯化。只有在存在還原劑的條件下,才能氯化TiO2。
最初反應(yīng)的熱量來自于電加熱,采用碳電阻塊,但反應(yīng)一旦開始后,氯化反應(yīng)將放出足夠的熱量,無需進(jìn)一步外部加熱。事實上,為了控制氯化溫度,加入氯化器的焦和鈦原料的量必須精確。如果氯化器的溫度太低,原料中的TiO2轉(zhuǎn)化成TiCl4將不充分,而且未反應(yīng)的氯氣將通過氯化器。如果溫度太高,流態(tài)化床的材料將融化,氯化器將被“堵塞”。
杜邦獨有使用鈦鐵礦/白鈦石混合原料的技術(shù)和商業(yè)能力,其TiO2品位低達(dá)60%。其他所有鈦白生產(chǎn)商要求原料配料的品位為85%,這使他們的原料受到限制,只能使用金紅石、人造金紅石和/或從鈦鐵礦富集而來的鈣、鎂含量很低的鈦渣。CaO和MgO含量要求很低是因為這些物質(zhì)在氯化溫度下將形成液態(tài)氯化物,削弱流態(tài)化床的性能并可能堵塞出口管道。鈦原料中的氧化錳雜質(zhì)也有同樣的風(fēng)險,盡管其程度要低一些。
氯化器釋出的氣流不僅含有TiCl4和碳氧化物,而且含有焦粉塵和各種由初始原料中雜質(zhì)形成的氯化物,主要是FeCl3、SiCl4、ZrCl3、MnCl2、VOCl3。氣流離開氯化器后,經(jīng)過過濾器除塵。在一些工廠,氣流隨后通過200℃的冷凝器除去大部分的FeCl3。如果鈦鐵礦/白鈦石用作初始原料,這一階段將產(chǎn)生大量的FeCl3。
出現(xiàn)了廢物處理問題。
B、冷凝與提純
離開氯化器的氣體,通過噴以預(yù)先液化的物質(zhì)快速冷卻并冷凝。其目的是使溫度降到接近于TiCl4的沸點溫度—136℃。在此溫度下,F(xiàn)eCl2、MnCl2?、CaCl2和MgCl2以固體物質(zhì)形式分離出來,并能被除掉。
冷凝物—主要是TiCl4—仍含有雜質(zhì),這些雜質(zhì)的沸點溫度與TiCl4相似。它們包括:SnCl4、SiCl4、AsCl3、AlCl3和VOCl3。成功運行一個氯化法鈦白廠,使這些雜質(zhì)的含量降至最低是一關(guān)鍵問題。
VOCl3常常通過與銅或礦物油復(fù)合分離出來。另一種方法是用H2S在90℃時處理不純的TiCl4,將VOCl3還原成VOCl2(其沸點相當(dāng)高),并以硫化物形式析出剩余的鐵和釩。AlCl3通常被轉(zhuǎn)化成一種沸點較高的復(fù)合鹽,這樣便易于分離了。
TiCl4在過濾掉殘余物后,通過進(jìn)一步精確控制的蒸餾最終提純。由于可以獲得相對純凈的TiCl4,鈦白生產(chǎn)的氯化法工藝非常具有吸引力。商業(yè)級TiCl4,不論是外供產(chǎn)品還是鈦白生產(chǎn)商生產(chǎn)的中間產(chǎn)品,其純度一般為98.5%。微量雜質(zhì)主要是COCl2、SiCl4和VOCl3。
C、氧化
下一步驟是用空氣和或氧氣氧化TiCl4,產(chǎn)出純TiO2和釋出氯氣。低于600℃時,氧化反應(yīng)的速度可以忽略不計,但高于此溫度,反應(yīng)速度將迅速提高。一般采用的反應(yīng)溫度范圍為1300℃-1800℃。
在將TiCl4氧化成適于鈦白應(yīng)用(其粒度控制非常嚴(yán)密)的TiO2產(chǎn)品還存在若干問題??朔@些問題的方法是極其重要的、受到現(xiàn)有生產(chǎn)商嚴(yán)密保護的技術(shù)決竅。這些問題對于想進(jìn)入鈦白行業(yè)興建氯化法廠的新生產(chǎn)商來說是主要障礙。
在反應(yīng)溫度下,氯氣和四氯化鈦都有極強的腐蝕性。所以氯化器常用不銹鋼制成并襯有耐火材料?,F(xiàn)代化的鈦白廠使用的氯化器一般高度為10-15m,直徑為4-9?m。這種對昂貴的耐腐蝕材料的需求提高了興建氯化法鈦白廠的投資水平。
氧化反應(yīng)必須在氣相中進(jìn)行,而且最好是溫度剛剛超過600℃。因此,防止TiCl4冷凝到反應(yīng)器壁上至關(guān)重要。通常用較大的反應(yīng)空間并在TiCl4入口周圍連續(xù)不斷地導(dǎo)入惰性氮氣流,可以達(dá)到此目的。
在使用克爾-麥基技術(shù)的工廠中,氧化是在常壓下進(jìn)行的。這就要求使用專門的氯氣壓縮器,這是將氯氣回收到氯化器中所必不可少的。
在使用由杜邦、克朗諾斯和美禮聯(lián)開發(fā)的技術(shù)的工廠中,氧化約在4個大氣壓下進(jìn)行。氧氣和TiCl4比氯氣更易壓縮,因此施壓的反應(yīng)物為將氯氣回收到氯化器中提供了有效的能量。
通??藸?麥基技術(shù)可以使鈦白粒度分布很集中,但其它氯化法工藝通過對后處理段的精心設(shè)計彌補了其不足之處。
氧化反應(yīng)放出的熱不足以維持最佳的反應(yīng)溫度,因此必須額外供熱。一種方法是TiCl4和混有少量蒸氣的氧氣/空氣被分別加熱到所需的溫度,通過各自的輸入口導(dǎo)入經(jīng)預(yù)熱的反應(yīng)器。另一種方法是通過燃燒一氧化碳產(chǎn)生熱的CO2進(jìn)行額外供熱,這另需一單獨的一氧化碳輸入口。第三種方法是氧氣經(jīng)電火花加熱并用等離子火焰槍導(dǎo)入反應(yīng)器。
生產(chǎn)的TiO2在高溫下的保留時間必須非常短暫,否則,其粒子將長得很粗,因此,通過噴射液態(tài)和氣態(tài)形式的冷凍TiCl4和氯氣使載送細(xì)微TiO2粉末的氣體快速冷卻。有一種方法是讓輸入的TiCl4和氧氣經(jīng)過熱的二氧化硅流態(tài)化床,細(xì)微的TiO2粉末將被未反應(yīng)的氣體和釋出的氯氣所帶走。
為增加TiO2的收率,需在能形成TiO2粒子的地方周圍加固體晶核。為此,有時將氯化鋁(AlCl3)加到TiCl4的進(jìn)料裝置中。氯化鋁氧化成氧化鋁(Al2O3),以細(xì)粒形式固化,提供了所需的晶核劑。輸入的空氣/氧氣氣流中所帶的少量蒸汽在快速冷卻階段形成水滴,這也可起到晶核的作用促進(jìn)TiO2粒子的形成。
必須防止在反應(yīng)器壁上、氣體入口噴咀和其它表面形成大量TiO2沉積物。這在流態(tài)化床工藝中尤其困難,因為固體TiO2易于堆積在二氧化硅床上,而不易完全被氣體所帶走。在有些廠中,將氮氣流連續(xù)導(dǎo)至反應(yīng)器的入口處,以保持其冷態(tài)并防止TiO2沉積物的堆積。而另一些廠,在氧化反應(yīng)器的末端裝有一鈦白冷卻管。冷卻管壁不斷用砂或磨料打磨。
經(jīng)過快速冷卻后,用普通的旋風(fēng)、袋式或靜電除塵器將微細(xì)的TiO2從氣體中收集起來。排放的氣體進(jìn)入冷凝器以回收氯氣?;厥盏穆葰庖砸簯B(tài)形式保存待再次用于前面的工段。
除塵器上捕集的TiO2含有大量的吸附氯,通過加熱或更通常的蒸汽處理除去,洗掉的氯被轉(zhuǎn)化成了鹽酸。最后,用含硼酸0.1%的蒸汽進(jìn)一步處理,消除微量的氯和吸附在TiO2粒子上的鹽酸。
然后,使TiO2粒子脫離過濾器并用水打漿。通過濕磨粉碎聚集顆粒和團塊,待包膜和后處理。
?
七、?介紹國內(nèi)外鈦白行業(yè)基本情況
1、國外情況簡介
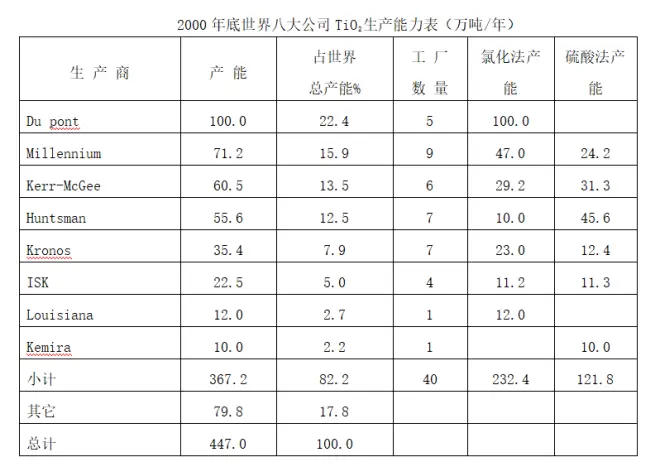
?
據(jù)資料報道,由于對TiO2工業(yè)前景的繼續(xù)看好,國外某些鈦白生產(chǎn)商正在計劃脫瓶頸擴產(chǎn)工程,預(yù)計到2003年,全球的鈦白產(chǎn)能每年將增加20萬噸左右,達(dá)到約510萬噸。其中包括:Huntsman計劃將位于英國Greatham的產(chǎn)能擴大一倍和Huelva的產(chǎn)能增加1.5萬噸工程,Kemira在Pori的2萬噸擴產(chǎn)計劃,Sachtleben在Duisberg的1.5萬噸擴產(chǎn)計劃,Du pont在美國新約翰遜維爾的6.5萬噸擴產(chǎn)計劃及中國鈦白生產(chǎn)商的擴。
杜邦公司
杜邦是世界頭號鈦白生產(chǎn)商,總部位于美國德拉維爾的Wilmington。其產(chǎn)能超過100萬噸/年,在該行業(yè)全球總量中略低于23%。該公司有5個工廠,全部獨資,而且都采用杜邦的氯化法技術(shù)。各廠2000年底的產(chǎn)能(以千噸/年計)如下所列:
阿爾塔米拉,??墨西哥?????????120
迪萊爾,??????美國密西西比???285
埃奇莫爾,????美國德拉維爾, 135
新約翰遜威爾,美國田納西,???380
觀音,?????????臺灣??????????110
合計 ????????????????????????1030
鈦白是杜邦最重要的產(chǎn)品之一,占公司營業(yè)總收入的6%—8%。杜邦在鈦白工業(yè)成功背后的關(guān)鍵因素之一是其獨一無二的技術(shù)能力,即可以氯化等級相對較低的原料配料,TiO2的品位可低達(dá)60%。與氯化低等級原料相關(guān)的是杜邦獲得了許可采用深井處理其迪萊爾廠產(chǎn)生的大量酸性氯化物廢物和采用特定的方式處置阿爾塔米拉工廠的廢物。時至近日,新約翰遜威爾工廠的經(jīng)濟效益一直還得益于采用深井技術(shù)處理生產(chǎn)鈦白所產(chǎn)生的廢物。
美禮聯(lián)化工公司
美禮聯(lián)公司(位于倫敦和美國新澤西州的雷德邦克)是世界第二大鈦白生產(chǎn)商。美禮聯(lián)目前有9個獨資鈦白廠,超過了同行業(yè)中其它任何一家公司,其中5個是氯化法廠,4個是硫酸法鈦白廠,這些廠的合計產(chǎn)能接近75萬噸/年,氯化法鈦白的產(chǎn)能約占70%。各廠2000年底的產(chǎn)能(以千噸計)如下:
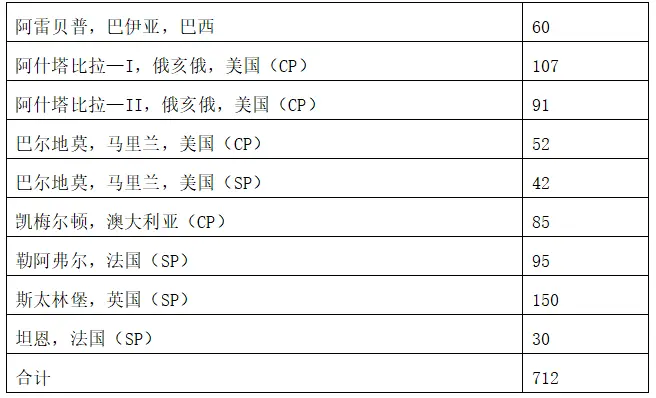
Huntsman Tioxide
1999年6月30日,Huntsman公司(位于尤他州的鹽湖城)取得了對Tioxide、ICI的全球聚氨酯業(yè)務(wù)和經(jīng)挑選的石化資產(chǎn)的主要控制權(quán)。
Huntsman在鈦白行業(yè)并不領(lǐng)先,但隨著Tioxide的收購卻一躍成為世界前四大TiO2生產(chǎn)商之一,占全球產(chǎn)能的12.6%。Huntsman?Tioxide有6個獨資工廠,另在南非有個控股60%的工廠,在美國還有個持股50%的工廠。這些工廠在2000年底的產(chǎn)能如下(以千噸/年計):
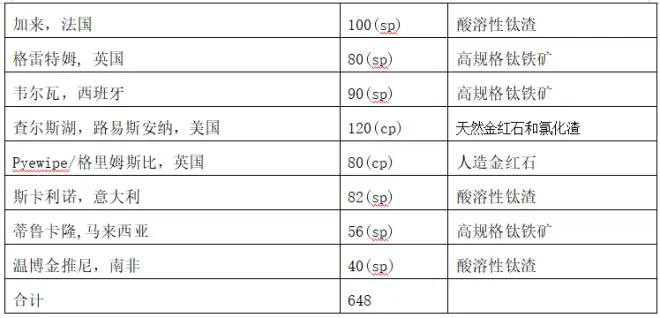
克爾-麥基公司
?????克爾-麥基公司位于美國俄克拉荷瑪城,近幾年來,為鞏固其世界前四大鈦白生產(chǎn)商之一和重要的中型油氣生產(chǎn)商的地位,進(jìn)行了幾次重大的收購活動。?
如今,克爾-麥基有6個全資鈦白廠,其中3個為最近收購的硫酸法鈦白廠,3個為采用克爾-麥基氯化法技術(shù)的氯化法廠。另外,公司在西澳大利亞的一個從礦砂到鈦白的一條龍綜合性合資公司中還擁有50%的股份,該合資公司有一個采用克爾-麥基氯化法技術(shù)的鈦白廠。2001年在奎那納最近一次擴建完成后,克爾-麥基七個廠的現(xiàn)有總產(chǎn)能為61.4萬噸/年,其中氯化法鈦白占70%。這七個廠2000年底的產(chǎn)能(以千噸計)如下:
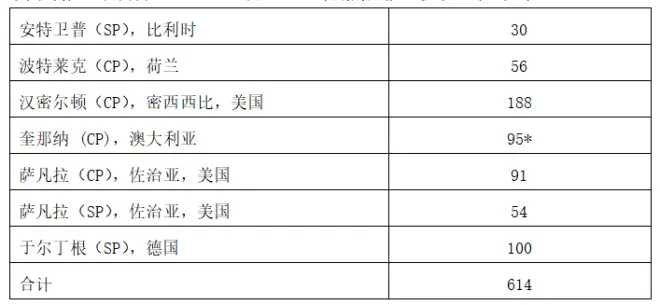
克朗諾斯公司
克朗諾斯公司(總部設(shè)在新澤西州的Cranbury)是NL工業(yè)公司(位于德州的Huston)唯一的全資子公司。
克朗諾斯是世界第5大鈦白生產(chǎn)商,其所屬總產(chǎn)能為44萬噸/年,占全球?10%份額。公司擁有4個獨資硫酸法鈦白廠,3個獨資氯化法鈦白廠和一個持股50%的氯化法鈦白廠。這些廠2000年末的產(chǎn)能(以千噸/年計)如下:
腓特烈斯塔?????????????挪??威 (SP)?????32
Langerbrugge ??????????比利時 (CP)?????65
查爾期湖,路易斯安那????美??國?(CP) ????60
萊沃庫森???????????????德??國?(CP) ????120
萊沃庫森???????????????德??國?(SP) ????20
瓦雷訥?????????????????魁北克 (CP)?????65
瓦雷訥?????????????????魁北克 (SP)?????18
合計 ??????????????????????????????????380
石原產(chǎn)業(yè)公司
位于大板的石原產(chǎn)業(yè)公司(ISK)是日本最大的鈦白生產(chǎn)商。該公司在三重縣四日市有一個10萬噸/年的硫酸法鈦白廠和一個5.5萬噸/年的氯化法鈦白廠;在新加坡裕廊有一個4.5萬噸/年氯化法鈦白廠。ISK在亞太市場的份額超過20%。
凱米拉鈦白公司
位于芬蘭波里的凱米拉鈦白公司是凱米拉集團(總部位于赫爾辛基)下屬的全資子公司。凱米拉集團如今的年銷售收入約為24億歐元,其中鈦白所占比例略低于10%。
海外工廠出售后(美國薩凡納和荷蘭),在波里的12萬噸/年鈦白廠如今是凱米拉唯一的鈦白生產(chǎn)廠,最近,凱米拉宣布將于2002年前將產(chǎn)能擴增至13萬噸/年。從中期看,其產(chǎn)能將在2005年前進(jìn)一步擴至15萬噸/年。凱米拉的生產(chǎn)將主要針對其擅長的領(lǐng)域,包括印刷油墨領(lǐng)域。
薩其賓化工公司
薩其賓化工公司(位于德國的杜易斯堡)是戴納米特-諾貝爾(位于特羅伊斯多夫)的全資子公司。而戴納米特-諾貝爾又是MG技術(shù)集團的全資子公司。MG技術(shù)集團(總部位于法蘭克夫)即為以前的金屬公司,在成功完成由原材料導(dǎo)向的綜合性企業(yè)向富有創(chuàng)新精神的技術(shù)集團轉(zhuǎn)型后,于2000年4月14日變更為現(xiàn)在的名稱。薩其賓的鈦白業(yè)務(wù)占銷售收入的75%以上,其余的收入來源于立德粉、鋇顏料、鋅顏料、多鋁氯化物、水處理劑和各類特種化學(xué)制品。
在世界鈦白行業(yè)中,薩其賓一直是重要的中型生產(chǎn)商,特別是在人造纖維消光用銳鈦型鈦白、防紫外線化妝品用納米鈦白、汽車漆用鈦白、木材和皮革拋光用鈦白以及其它特定用途的鈦白供給方面, 起著主導(dǎo)作用。薩其賓是世界第八大鈦白生產(chǎn)商,其杜易斯堡-洪貝格硫酸法鈦白廠的產(chǎn)能10萬噸/年,所用原料為鈦渣和一定量的鈦鐵礦。
2、國內(nèi)情況簡介
2003年國內(nèi)鈦白行業(yè)前21位情況統(tǒng)計
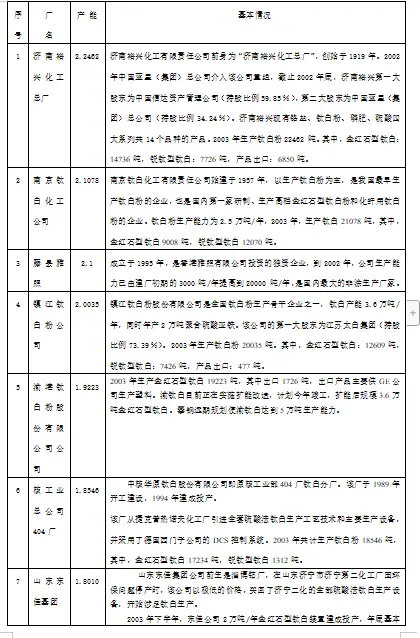
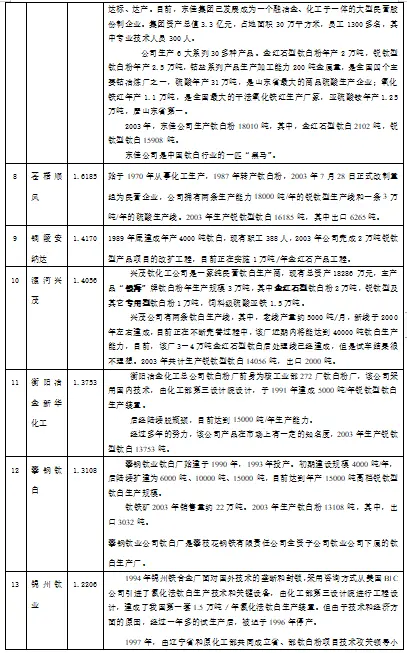
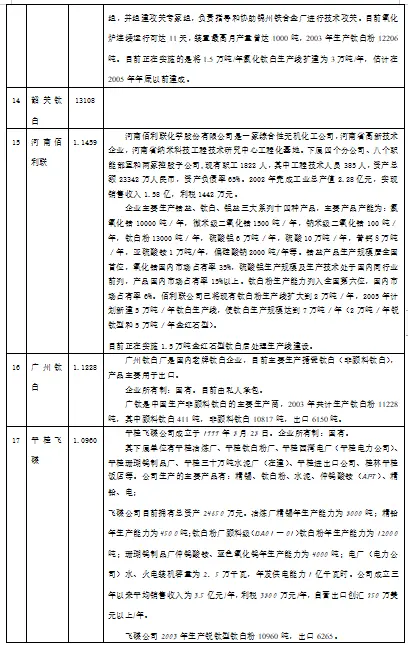
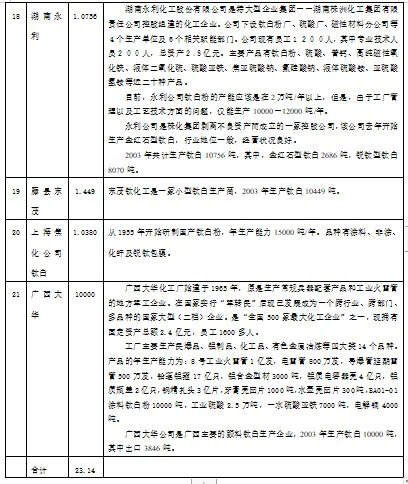
據(jù)了解,今后幾年國內(nèi)鈦白粉的產(chǎn)能擴張還將繼續(xù),除國內(nèi)企業(yè)的擴建和新建外,國外鈦白生產(chǎn)商也對中國巨大的市場表示出了濃厚的興趣,如美國亨茲曼(Huntsman)公司擬在我國建設(shè)氯化法鈦白工廠,并已在國內(nèi)進(jìn)行了長時間的廠址考察工作。我國鈦白工業(yè)真正進(jìn)入了規(guī)??涨暗陌l(fā)展時期。
?
八、?各崗位的目的、工藝流程及原理、設(shè)備配置、原輔動力要求、主要控制參數(shù)、操作要點、故障處理、計算及現(xiàn)場檢測項目
(一)?雷蒙崗位
1、?目的
鈦精礦一般粒度比較粗,比表面積較小,酸解時與硫酸接觸面積小,不易被硫酸有效地分解。因此,在使用前必須將其磨細(xì),以增加反應(yīng)接觸面,使酸解反應(yīng)能夠正常進(jìn)行。
參加酸解反應(yīng)的礦粉不僅必須達(dá)到一定的細(xì)度,而且粒度分布要求窄而均勻,這樣才能得到較高的酸解率,得到符合工藝要求的硫酸鈦液。一般礦粉細(xì)度要求為:325目 篩余≤1.5%。
2、?粉碎的工藝流程
????鈦精礦由斗提式提升機送入貯料斗,再由給料裝置將原礦定量、均勻、連續(xù)地送入雷蒙磨進(jìn)行粉碎。已被粉碎的物料由鼓風(fēng)機鼓入的空氣流從分析器帶出,粗顆粒被擋后落入粉碎區(qū)域重新返回雷蒙磨構(gòu)成閉路循環(huán)。分離出的物料自旋風(fēng)分離器下部卸出,進(jìn)入礦粉中間貯槽,再由人工裝袋,用卷揚機提升送至礦粉貯槽,供酸解使用。
????部份循環(huán)風(fēng)經(jīng)布袋收塵器除塵后排空,收塵下來的飛粉進(jìn)入礦粉中間貯槽。
3、?粉碎設(shè)備
雷蒙磨國內(nèi)常用的設(shè)備,是一種擺輪式研磨機,靠擺輪的重力膠離心力,對鋼圈所產(chǎn)生的擠壓和研磨作用達(dá)到粉碎物料的目的。我廠使用的是5R3216型雷蒙磨(5R:五輥;32:磨輥直徑32cm;16:磨輥高度16cm)。
雷蒙機的工作原理是:雷蒙主機內(nèi)裝有磨環(huán)和磨輥,磨環(huán)固定在機座上,磨輥則自由懸掛在豎軸頂端的十字形懸輥架上,磨輥既能繞中間豎軸旋轉(zhuǎn)又能自轉(zhuǎn)。雷蒙機運轉(zhuǎn)時,磨輥在離心力作用下緊貼在磨環(huán)表面對加入物料產(chǎn)生擠壓和研磨作用而使其粉碎。未被粉碎的物料墜于機底,并被鏟刀鏟起重新將其拋擲于滾動很快的磨輥前的磨環(huán)面上,已被粉碎的物料由空氣流攜出??諝饬饔蓹C底上吹,使粉碎后物料通過分析器分級,細(xì)度合格的進(jìn)入旋風(fēng)分離器中,細(xì)度不合格的再返回雷蒙磨重新研磨。轉(zhuǎn)速越大,粒度越細(xì);反之則粒度越粗。
粉碎細(xì)度可由調(diào)節(jié)吹入的空氣量的大小及分析器的轉(zhuǎn)速等控制。
4、原輔動力要求
1)?電源:220V/50Hz
2)?礦粉
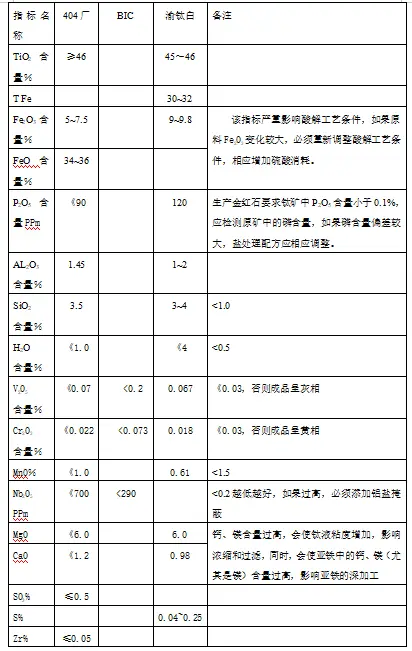
?
5、主要控制參數(shù)及影響因素
1)操作條件
????雷蒙主機:電壓?380v?電流?≤110A
????鼓風(fēng)機:電壓?380v?電流?≤100A
分析機轉(zhuǎn)速:650-850r/min
2)質(zhì)量指標(biāo)
礦粉細(xì)度??+325目3~5%???礦粉水份<0.5%
3)影響原礦粉碎的因素主要有以下幾種
1)?進(jìn)料量:加料量過大,不僅礦粉細(xì)度難以達(dá)到工藝要求,而且使主機負(fù)載增加,并易堵塞雷蒙磨,使粉碎不能順利地進(jìn)行。通??刂萍恿狭繛?.0-1.1t/h。
2)?分析器轉(zhuǎn)速:分析器轉(zhuǎn)速過高,礦粉過細(xì),不僅降低雷蒙磨的粉碎能力,而且酸解時易導(dǎo)致冒鍋等事故的發(fā)生;分析器轉(zhuǎn)速過低,礦粉細(xì)度不能達(dá)到工藝規(guī)定的要求,影響酸解反應(yīng),降低酸解率。
3)?風(fēng)量:鼓入風(fēng)量過大,不僅礦粉細(xì)度達(dá)不到要求,而且使礦粉粒度分布過寬,影響酸解的正常進(jìn)行;鼓風(fēng)量過小,影響雷蒙磨的生產(chǎn)能力。
4) 原礦的濕度:濕度過大,物料在輸送過程中易堵塞。
6、操作要點
1)啟動分級器。在風(fēng)機及引風(fēng)機正常后,開啟雷蒙主機。
2)控制加料量在1.5-2.5t/hr。
3)根據(jù)產(chǎn)出礦粉質(zhì)量調(diào)節(jié)分級器轉(zhuǎn)速。
4)隨時檢查礦粉細(xì)度,確保質(zhì)量指標(biāo)。
7、異常情況處理
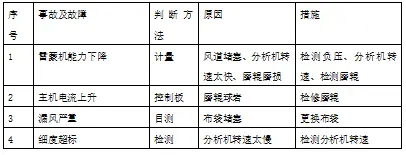
?
(二)?酸解
1、?目的
使鈦精礦中的有用組份轉(zhuǎn)變成可溶性狀態(tài),或易于反應(yīng)的狀態(tài),或使精礦破壞分解為
簡單的化合物,然后制成含鈦溶液而與各種雜質(zhì)分離。
2、酸解工藝流程或原理
酸解作業(yè)是在耐酸瓷磚的酸解罐中進(jìn)行的。將濃度為92-94%的濃硫酸裝入酸解罐中并通入壓縮空氣,在攪拌的情況下加入磨細(xì)的鈦精礦。精礦與硫酸的混合物用廢酸稀釋誘發(fā)酸解主反應(yīng)的進(jìn)行,主反應(yīng)結(jié)束后,讓生成的固相物在酸解罐中熟化,使鈦精礦進(jìn)一步分解,分解后所得固相物基本上是由鈦鐵硫酸鹽和一定數(shù)量的硫酸組成。固相物冷卻到一定溫度后,用水浸出,并用壓縮空氣攪拌,浸出完全以后,浸出溶液用鐵屑還原,將溶液中的硫酸高鐵還原成硫酸亞鐵。
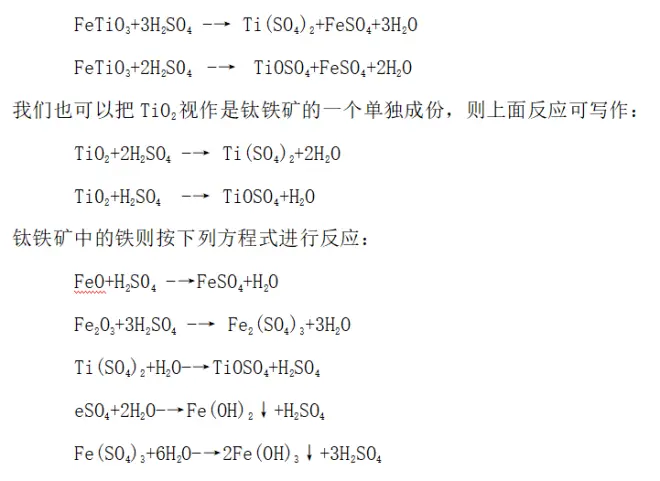
? ? ??
3、酸解設(shè)備
酸解鍋φ3460×(3600+3070)+鍋蓋550+分布板厚度300,材質(zhì)是A3鋼搪鉛再襯
雙層瓷磚。
4、?原輔動力要求
壓縮空氣總壓力: ????????≥0.4MPa
浸取水水溫: ???????????25℃
蒸汽壓力: ??????????????0.40-0.60Mpa
廢酸濃度:???????????????≥180g/l
礦粉:??????????????????細(xì)度:325目篩余物:3~5% ???含水量:<0.5%
還原劑指標(biāo):
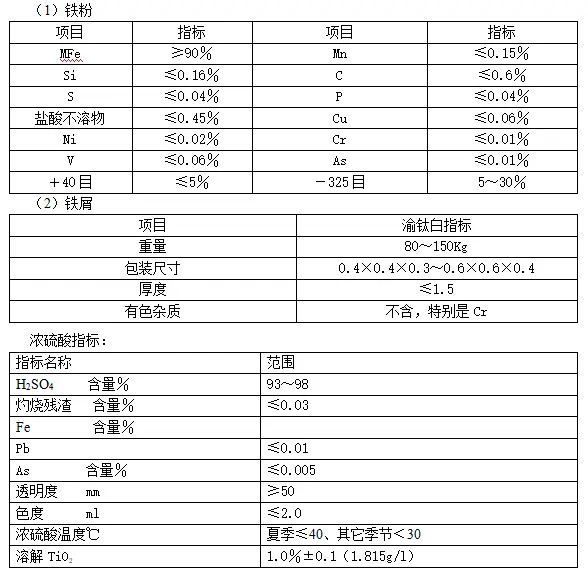
5、?主要控制參數(shù)
1)質(zhì)量技術(shù)指標(biāo)
鈦液比重????????????????48-52Be'
酸解率??????????????????≥94%
總鈦????????????????????115-135g/l
F值?????????????????????1.75-1.85
Ti3+ ?????????????????????1-3g/l
穩(wěn)定度??????????????????≥300
2) 操作條件
酸礦比: ????????????????1.52-1.56
每鍋投料量??????????????礦粉?8800±50kg
原料硫酸濃度????????????≥92.5%
反應(yīng)酸濃度??????????????84-88%
加鐵粉量????????????????640-800kg ???????????????金屬鐵含量:≥90%
酸礦混合時間: ??????????30分鐘
成熟時間: ?????????????夏季40~60min, 冬季30min
浸取時間: ?????????????≥4h
酸礦混合溫度: ?????????夏季≤40℃,冬季≤45℃
主反應(yīng)引發(fā)溫度: ????????110℃
浸取及還原溫度??????????65-70℃
放料溫度????????????????夏季:60-65℃?冬季:65-70℃
酸礦混合壓空壓力: ??????0.06-0.08MPa
主反應(yīng)壓空壓力: ????????0.04-0.06MPa
浸取壓空壓力: ??????????0.08-0.10MPa
還原壓空壓力: ??????????0.04-0.06MPa
小度水加量: ????????????4.0-8.0m3
廢酸加量: ?????????????3.0-3.5m3
水加量 ?????????????????23~26m3?
放料體積: ??????????????≥28m3
3)影響浸取速度的主要因素
(1)固相物的多孔性
????反應(yīng)后的固相物是呈海綿狀的多孔性物質(zhì),這些物質(zhì)遇水后,由于水滲入微孔內(nèi)部,接觸面大,因此,極易溶解并放出熱量。如果得到的固相物比較“硬板”,多孔性差,浸取就比較困難。
(2)固相物的溫度
????固相物的溫度高有利于浸取,但是溫度高于80℃,在加水浸取時溶液溫度太高,易使溶液的穩(wěn)定性變差甚至發(fā)生早期水解。
(3)浸取液的濃度(比重)
????一般來說浸取液的比重越高則浸取越慢,但濃度不能過低,過低地隨后的過程中容易發(fā)生早期水解。同時也會對以后水解產(chǎn)物的結(jié)構(gòu)產(chǎn)生不良影響,或者會增加濃縮的工作量。
(4)是否有早期水解
????固相物如有不同程度的早期水解,浸取時就有大量“僵塊”,溶化不掉,影響浸取速度。
(5)加浸取水的速度
????加浸取水的速度要與固相物溶解速度相適應(yīng)。一般來說設(shè)備大,要加得快,設(shè)備小要加得慢一些。
4)影響酸解率的主要因素
(1)酸礦比
????硫酸配比越高,反應(yīng)越完全,酸解率也越高,但是過高酸礦比會使硫酸單耗上升。相對而言,對酸解率的提高卻相差不多。
(2)礦粉粒度
????礦粉越粗,反應(yīng)越慢,甚至有些粗粒不反應(yīng),就影響酸解率。
????礦粉粒度不勻也會影響酸解率。在反應(yīng)時,細(xì)粒首先反應(yīng),粗粒尚未反應(yīng),當(dāng)增加熱量至粗粒開始反應(yīng)時,則已反應(yīng)部分可能會有早期水解。
(3)硫酸反應(yīng)濃度
????硫酸反應(yīng)必須適當(dāng)。濃度太低則反應(yīng)溫度低,反應(yīng)也不完全;而太濃則發(fā)熱量太高,會產(chǎn)生早期水解。硫酸濃度過高和過低,均會影響酸解率。
(4)攪拌程度
????反應(yīng)前如攪拌不勻,有未打散的礦粉團塊,會影響酸解率;如攪拌太猛,過多地濺在鍋壁四周,此部分熱量不夠,便無法反應(yīng),也會影響酸解率。
(5)反應(yīng)的溫度
????據(jù)某廠介紹,主反應(yīng)結(jié)束后,如立即停止吹風(fēng),以免降低反應(yīng)物的溫度,可以提高酸解率。
(6)成熟時間
????一般成熟時間越長,酸解率便越高,但由于固相物溫度降低,會使溶解速度變慢,對浸取不利。
(7)早期水解
????如果發(fā)生早期水解,則酸解率便要下降。
6、?操作要點
6.1 ?通知備礦崗位將礦粉送入礦粉儲斗。
6.2??將酸泵入硫酸計量桶中,酸計量好后,檢查其它酸解鍋的進(jìn)酸閥門是否關(guān)好。開相應(yīng)酸解鍋壓空閥門,再開相應(yīng)酸解鍋進(jìn)酸閥門,開酸計量桶閥門將酸送入酸解鍋,進(jìn)完酸后,關(guān)進(jìn)酸閥門。
6.3 ?打開礦粉儲斗的插板閥,放完礦粉后,繼續(xù)攪拌30分鐘。
6.4 ?檢查其它酸解鍋的進(jìn)稀釋廢酸閥門是否關(guān)好。調(diào)整壓空壓力后,開稀釋廢酸計量桶閥門,加入計量的或廢酸。
6.5 ?如果需要,打開蒸汽閥門,引發(fā)主反應(yīng)。
6.6 ?待酸解鍋出現(xiàn)輕微震動時,關(guān)閉蒸汽閥門。
6.7??主反應(yīng)開始時,啟動尾氣處理系統(tǒng)。主反應(yīng)結(jié)束后,關(guān)閉尾氣處理系統(tǒng)。
6.8??主反應(yīng)結(jié)束后,繼續(xù)吹壓空1~3min,然后調(diào)整小壓空壓力,成熟30~60min。
6.9??成熟結(jié)束后,先用廢酸上浸,再用水底浸至淹沒固相物,然后再用上浸,依次加入水、小度水浸取固相物,控制好加水速度,?使整個浸取過程時間控制在50min-60min,浸取完后鈦液溫度為65-70℃,玻美度為39-42Be',浸取時需控制好浸取體積。
6.10?浸取完后,調(diào)大壓空壓力,每隔1小時測一次鈦液溫度、玻美,如溫度過低,則通入蒸汽,保持鈦液溫度為65-70℃,若玻美≥50Be',則加入適當(dāng)小度水或水將玻美調(diào)至46-48Be'。
6.11?在放料前90-120min控制鈦液溫度60-65℃,加入鐵絲,鐵絲充分還原后,在放料前30min用硫氰酸銨和硫酸高鐵氨檢查鈦液中三價鈦是否達(dá)標(biāo),如果三價鈦未達(dá)標(biāo),則補加一定量的鐵粉至三價鈦達(dá)標(biāo),開始通知凈化崗位放料。注意出現(xiàn)三價鈦之后適當(dāng)調(diào)小壓空壓力。
6.12?放料前取樣化驗,如總鈦過高,可加入小度水或水進(jìn)行調(diào)節(jié),如F值低,可加入廢酸或濃酸調(diào)節(jié)。
6.13?放料前測鈦液溫度,將溫度控制在所需范圍內(nèi)放料。
7、?異常情況處理
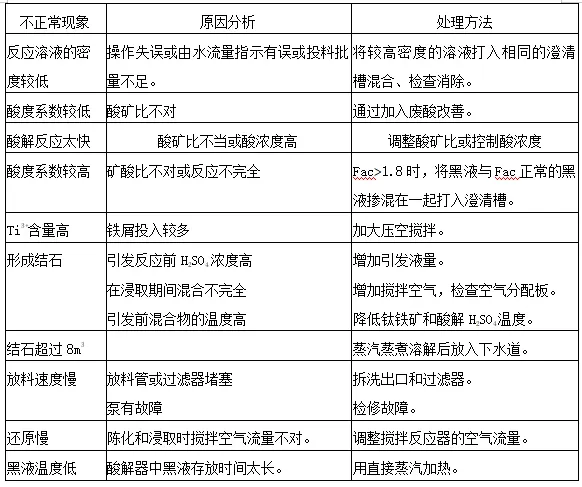
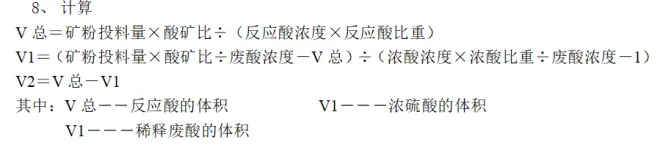
9、?現(xiàn)場檢測項目
每批檢測Ti+3。
?
(三)?凈化
1、目的
通過沉降除去雜質(zhì),可提高副產(chǎn)品硫酸亞鐵的質(zhì)量并加快鈦液的過濾速度。同時膠體微粒如不除去,在以后水解時便成為一種無一定組成和數(shù)量的晶核,會影響水解過程和水解產(chǎn)物的結(jié)構(gòu)。
2、凈化工藝流程或原理
沉降是適用于從粗分散體系懸浮液中分離出固體顆粒的方法,它是利用重力作用使體系
中的懸浮固體顆粒沉降下來。對于鈦液中屬粗分散體系的懸浮殘渣,可通過沉降而分離出來。然而對于粒徑為1-10μm的細(xì)不溶雜質(zhì)和屬細(xì)分散體系的膠體顆粒,則由于布朗運動,重力不能使之沉降.前者由于鈦液粘度很大,使顆粒懸浮在體系中相對穩(wěn)定。后者由于膠粒在鈦液中吸附H+而帶有相同的正電荷,因而具有靜電排斥力,并在膠體周圍形成了溶劑化的漫散雙電層,十分穩(wěn)定,不能相互凝聚。
3、沉降設(shè)備
10.5×6.5×2.42+17m3,整體襯8層波力布,底部再襯一層瓷磚。沉降設(shè)備的生產(chǎn)能力與它的高度無關(guān),僅與水平截面積和顆粒的沉降速度有關(guān),而沉降速度又僅與微粒的大小、重量以及介質(zhì)的重度與粘度有關(guān)。
4、原輔動力要求
1)真空度≥0.04Mpa
2)總鈦115-135g/L ???溫度60-65℃???三價鈦1-3g/l???穩(wěn)定性≥250???
F值1.75~1.85
5、主要控制參數(shù)
1)質(zhì)量控制指標(biāo)
固含量≤0.2g/L??????????????抽速≤3min
2)操作條件
絮凝劑使用濃度1‰,加量15-25L/m3鈦液。
3)影響沉降的因素
(1)鈦液的比重
????一般來說隨著比重的升高,鈦液效果逐步變壞??梢哉J(rèn)為隨著比重上升絮凝顆粒與液相比重差縮小,顆粒沉降崐速度變慢,另外可以認(rèn)為,隨著鈦液比重的上升,溶液的粘度增加,粒子也就不容易沉降。比重一般控制在1.52-1.53。
(2)鈦液的溫度
????鈦液的溫度對沉降效果的影響也十分顯著。溫度上升,鈦液的粘度下降,有利于顆粒沉降。但對鈦液來說,溫度上升,穩(wěn)定性會下降,所以需要選一個適當(dāng)?shù)臏囟?,一般控制?0±5℃。
(3)鈦液的質(zhì)量
????隨著鈦液F值和穩(wěn)定性的提高,三價鈦含量的上升,可使沉淀效果提高。這是由于F值高,穩(wěn)定性好,鈦液中的膠體物便少,而三價鈦能使凝聚作用增強。如果沒有三價鈦便可能有大量FeO+和高鐵離子存在,這對沉降不利,因為它們能使膠粒的穩(wěn)定性增強。三價鈦濃度過高,會使鈦液粘度過大,也不利于沉降。鈦液質(zhì)量對沉降好壞的關(guān)鍵是膠體的多寡及其穩(wěn)定程度。
(4)沉降劑質(zhì)量
????沉降效果依賴于沉降劑的質(zhì)量。對于合成高分子化合物,其分子量大小、貯存濃度與時間、配制水質(zhì)、降解與否等都會影響。為確保沉降質(zhì)量和提高適應(yīng)能力,往往數(shù)種沉降劑配合使用。按先后分別加入無機凝聚劑、明膠和高分子絮凝劑。
(5)沉降劑使用濃度
????沉降劑的使用濃度與沉降澄清效果關(guān)系甚大。高分子沉降劑使用濃度應(yīng)低一些,這樣沉降劑分散均勻、粘度小,與鈦液的接觸面大,絮凝沉降效果好。如果濃度過低,則發(fā)生高分子降解的幾率便大,影響貯存時間與沉降效果,同時會使鈦液濃度沖淡,對生產(chǎn)帶來不利。
????高分子聚合物的濃度對其分子在溶液中的形態(tài)有很大影響。濃度高時,高分子極性基團向內(nèi)呈卷曲球形,粘度大,在鈦液中難以分散,容易出現(xiàn)一層不沉降在鈦液表面的絮妝物,而喪失絮凝能力。所以,沉降效果隨著沉降劑使用濃度的加大而變壞。一般高分子沉降劑的使用濃度為0.3-0.5%。
(6)沉降劑的用量
????沉降劑用量是確保沉降效果的關(guān)鍵。沉降劑沉降效果再好,若用量不當(dāng)仍得不到良好的結(jié)果。用量過大,會對膠體顆粒起再分散的保護作用,大大削弱了沉降劑的效能。用量不足,則中和捕集膠粒和細(xì)顆粒的作用不完全,也得不到好的沉降效果。如加入帶負(fù)電荷的沉降劑,鈦液中帶正電荷的微粒很快被中和凝聚合物的但如果用量過大,負(fù)電荷發(fā)生過剩會使微粒重新帶上負(fù)電荷而又趨于穩(wěn)定,達(dá)不到沉降的預(yù)期目的。我廠現(xiàn)用絮凝劑加量15-20 l/m3。
(7)沉降劑加入順序
????對于使用凝聚劑和混合沉降劑,其加入順序?qū)Τ两敌Ч挠绊懸彩遣豢珊鲆暤?。如采用Sb2O3-FeS凝聚劑,若先加入FeS后加Sb2O3,沉降效果變得很壞。
(8)沉降操作
????在加入沉降劑之前,先進(jìn)行靜置粗沉,使鈦液溫度下降有利于初沉,細(xì)粒長大和正鈦酸復(fù)溶于游離酸中。從而可相對減少沉降劑的需要量,提高沉降效果。
6、操作要點
6.1接酸解放料通知后,打開酸解鍋底放料閥。
6.2 ?同時打開絮凝劑計量桶放料閥,并流進(jìn)入凈化池,調(diào)節(jié)流量至15-25 L/m3鈦液。
6.3 ?鈦液放凈后,關(guān)閉絮凝劑計量桶放料閥和酸解放料閥。
6.4 ?三小時后,從液面下0.3m處取樣自測凈化,合格后通知化驗室取樣,化驗結(jié)果出來后,通知板框崗位接料。
6.5 ?打開出料閥,啟動出料泵,將澄清鈦液送至清鈦液緩沖槽。
6.6??當(dāng)檢測鈦液凈化不合格時或清鈦液緩沖槽裝滿后,停出料泵,并將泵和管道的液體排凈。
6.7??沉降8批料后,將該凈化池中的殘余鈦液倒入其它的凈化池,打開池底泥漿閥,啟動泥漿泵,
將泥漿送入泥腳儲存槽。
6.8??打完泥漿后, 用少量水沖洗凈化池,并用泥漿泵將沖洗水送入泥腳儲存槽,洗凈后關(guān)閉池底泥漿閥。
7、異常情況處理―――沉降困難的檢查步驟:
1)?聚丙烯酰胺溶液;
2)?用聚丙烯酰胺對樣品液進(jìn)行試驗;
3)?降低酸解液的比重;
4)?檢查三價鈦含量,含量高則沉降困難;
5)?檢查鈦礦質(zhì)量:是否為高度不可溶鈦礦;
6)?檢測是否發(fā)生早期水解。
8、計算
1)絮凝劑改性配方
PAM用量4kg
溶解用水約1000L
Na3PO4配成10%溶液,其加量以調(diào)節(jié)PH值為9-11為準(zhǔn)。
甲醛加量:10kg(36%-38%)
二甲胺加量:20kg(35%-40%)
2)絮凝劑加量的計算公式
V1=V2×C1
V1-------絮凝劑加入體積L
V2-------酸解鈦液體積M3
C1-------絮凝劑加入相對量L/M3,一般15-20?L/m3鈦液
9、現(xiàn)場檢測項目
每批檢測凈化合格情況。
?
(四)?泥漿處理
1、目的
回收鈦液,提高收率,同時降低泥漿的濕含量,便于運輸。
2、泥漿處理工藝流程或原理
?
3、泥漿處理設(shè)備
兩臺80M2廂壓機。
4、原輔動力要求
泥漿溫度?45-50℃ ???????蒸汽壓力﹥0.4Mpa?????????真空度≥0.04Mpa
5、主要控制參數(shù)
1)操作條件
????機頭壓力?<0.8Mpa?????????濾布型號621#
2)質(zhì)量控制指標(biāo)
濾液凈化:合格 ?????????
3)影響泥漿壓濾速度的因素
(1)泥漿溫度
泥漿溫度太低,泥漿壓濾速度慢;溫度太高,鈦液易發(fā)生早期水解。
(2)濾布的使用時間
半月用20%NaHCO3復(fù)蘇濾布一次;半年更換濾布一次。
6、操作要點
6.1 開啟蒸汽閥門將泥渣預(yù)熱到45-50℃后,關(guān)閉蒸汽閥門。
6.2 鋪好濾布,啟動壓緊裝置壓緊板框。
6.3?啟動泥渣壓濾泵將泥漿打入壓濾機,濾液進(jìn)入凈化池。
6.4?當(dāng)機頭壓力達(dá)到0.8MPa時,關(guān)閉泥渣壓濾機泥漿入口閥。
6.5?松開板框,將濾餅卸入卸料槽。
6.6?每班沖洗一次濾布。
7、異常情況處理

8、現(xiàn)場檢測項目
2小時檢查一次鈦液凈化情況。
?
(五)?熱過濾
1、目的
經(jīng)沉降的鈦液仍含有膠體和細(xì)小的機械雜質(zhì),它們的表面積可吸附重金屬離子,如不除
去,則在水解時會成為不良的結(jié)晶中心,使水解產(chǎn)物粒子長大,影響水合二氧化鈦粒子的大小和形狀,使最終成品的品質(zhì),特別是外觀白度顯著變壞。鈦液過濾的目的,就是除去這些雜質(zhì),使鈦液進(jìn)一步凈化。
2、熱過濾工藝流程或原理
?
3、熱過濾設(shè)備
兩臺80M2板框壓濾機。
4、原輔動力要求
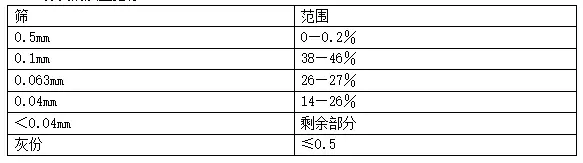
5、主要控制參數(shù)
1)?操作條件
????過濾壓力≤0.5Mpa。
糠灰加量0.5~0.75kg/m2。
????濾布型號240#。
????取樣周期30分鐘。
2)質(zhì)量技術(shù)指標(biāo)
總鈦:115-135g/l ???????F值:1.75-1.85 ?????????Ti3+:1-3g/l
穩(wěn)定度:≥300 ??????????固含量:0.02-0.04g/L ???凈化:合格
3)影響因素
?
6、操作要點
6.1 ?打開預(yù)冷卻器進(jìn)出水閥門,啟動冷卻水泵;打開預(yù)冷卻器進(jìn)出料閥門,同時啟動鈦液送料泵。
6.2 ?在木炭粉桶中放入1m3鈦液,同時加入60公斤糠灰攪拌30分鐘;再加入0.5m3鈦液攪拌30分鐘。
6.3 ?循環(huán)壓濾糠灰懸濁液,直至合格。
6.4 ?鈦液循環(huán)壓濾,直至合格。
6.5??開板框出料閥,正常出料。
6.6 ?正常出料過程中,每30分鐘必須作一次凈化綜合樣。
6.7 ?機頭壓力達(dá)到0.5MPa時,應(yīng)停機拆洗濾布。
7、異常情況處理
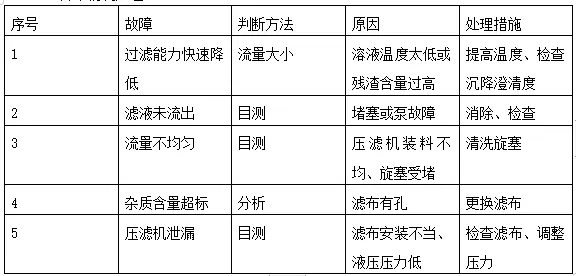
8、計算
G=0.75×M
其中:G――糠灰的量 ????????????????M―-板框的面積
9、現(xiàn)場檢測項目
半小時檢測一次凈化情況。
(六)?冷凍
1、目的
?
2、冷凍工藝流程或原理
在經(jīng)沉降所得到的熱鈦液中,各種硫酸鹽和磷酸鹽的溶解度是不同的而且與溫度有關(guān)。利用溶解度的這種差異,依據(jù)結(jié)晶原理,降低溫度,以降低FeSO4的溶解度,當(dāng)此溶解度低于溶液中的實際濃度時,便成為過飽和,其超過部分便會從鈦液中結(jié)晶析出,從而達(dá)到除去大量硫酸亞鈦的目的。
3、冷凍設(shè)備
12臺φ3280×4000,Vg=25m3。A3內(nèi)襯玻璃鋼+單層瓷磚。
4、原輔動力要求
冷凍水溫度??≤7℃
進(jìn)冷凍鍋稀鈦液溫度30℃-40℃
5、主要控制參數(shù)
1)質(zhì)量技術(shù)指標(biāo)
結(jié)晶終溫?10-15℃。
2)操作條件
3)影響因素
硫酸亞鐵晶體的顆粒大小和均勻程度,取決于晶核的生成速度、成長速度、單位體積中微晶碰撞的幾率、結(jié)晶表面的吸附作用及結(jié)晶的條件等。
????溫度是影響效果的主要因素,同時它還決定著結(jié)晶后鈦液的鐵鈦比(Fe+2/TiO2)。結(jié)晶終溫的確定除依賴于工藝要求的鐵鈦比外,還與室溫、硫酸亞鐵的分離洗滌設(shè)備、洗滌水溫與用量和技術(shù)操作水平等有關(guān)。一般控制在2-15℃。室溫控制在高限,反之亦然。載冷體與鈦液溫度差過大,攪拌勻或局部驟冷,都容易使換熱器的表面結(jié)晶出一層致密而厚的硫酸亞鐵層,嚴(yán)重影響冷卻效果。每次進(jìn)行結(jié)晶作業(yè)前應(yīng)該用水或汽清除硫酸亞鐵致密層,防止在冷凍初期鈦液與蛇管表面驟然接觸產(chǎn)生硫酸亞鐵致密層顯然是十分重要的。
????冷凍方式對硫酸亞鐵粒子的大小影響頗大。快速冷凍,由于硫酸亞鐵晶核生成速度大,所得晶體細(xì)?。恢鸺壚鋬?,使硫酸亞鐵晶核的生成速度,可得到大小均勻適度、利于分離與洗滌的晶體,逐級冷凍卻速度越慢,得出的晶體越粗。
????攪拌形式與攪拌速度對結(jié)晶效果也有影響。攪拌太快,硫酸亞鐵顆粒過細(xì),給鈦液與硫酸亞鐵帶來麻煩。攪拌太慢,易產(chǎn)生局部過冷,使結(jié)晶致密,影響冷凍效果,產(chǎn)生的硫酸亞鐵會堆積在結(jié)晶底部,造成放料困難,嚴(yán)重時能迫使攪拌停止運轉(zhuǎn)。
????鈦液濃度,尤其是其中的硫酸亞鐵濃度對硫酸亞鐵結(jié)晶的影響應(yīng)予注意。加入適量磨細(xì)的干硫酸亞鐵,使結(jié)晶碰撞的或然率大,可獲得大小顆粒適宜的硫酸亞鐵晶體。
鈦液中所含不溶雜質(zhì)和膠體物的量對硫酸亞鐵結(jié)晶的影響也不可輕視。鈦液中膠體物多,Sb2S3過量,帶入不溶雜質(zhì),或漏入氯化鈣溶液,這些雜質(zhì)會被吸附在硫酸亞鐵晶面上,遮蓋著其表面的活性區(qū)域,使晶粒成長減慢而得到細(xì)粒晶體。
6、操作要點
6.1 ?關(guān)閉冷凍鍋底放料閥,打開需進(jìn)料的冷凍鍋進(jìn)料閥。
6.2 ?當(dāng)鈦液超出冷凍鍋體積1/4時,啟動攪拌。
6.3 ?冷凍鍋進(jìn)完料后,準(zhǔn)確測量鈦液溫度,為通冷凍水的閥門開啟度作準(zhǔn)備。
6.4 ?通冷凍水,高溫段50-38℃冷凍水閥門開啟度為整個閥門圈數(shù)的1/8,中溫段38-28℃冷凍水閥門開啟度為整個閥門圈數(shù)的1/4,低溫段28-10℃冷凍水閥門全開。高溫段、中溫段冷卻水每半小時測溫一次,低溫段每小時測溫一次。
6.5 ?到達(dá)終溫后通知抽濾接料,放完料后停攪拌,清洗鍋體及盤管, 關(guān)死冷凍放料閥。
7、異常情況處理
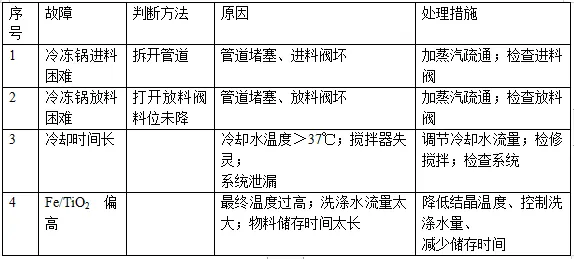
8、現(xiàn)場檢測項目
每小時檢測一次鈦液溫度。
?
(七)?亞鐵分離
1、目的
?
2、亞鐵分離工藝流程或原理
?
3、亞鐵分離設(shè)備
6臺8800×3800×1400,Vg=25m3。水泥現(xiàn)澆,內(nèi)襯玻璃鋼,底襯單層瓷磚。
4、原輔動力要求
真空度≥?0.05Mpa
鈦液接料溫度?10-15℃
5、主要控制參數(shù)
1)操作條件
濾布規(guī)格 ?化纖地毯。
使用要求 ?一層。
2)質(zhì)量技術(shù)指標(biāo)
鈦液質(zhì)量指標(biāo): Fe/TiO2 ?0.28-0.32?????總鈦?≥145g/l。
FeSO4.7H2O質(zhì)量指標(biāo): 純度?≥75% ??????殘鈦?≤0.5%。
3)影響因素
?
6、操作要點
6.1 ?通知冷凍崗位后,打開冷凍鍋放料閥放料。
6.2 ?將抽濾池進(jìn)滿鈦液,溢流鈦液進(jìn)入清鈦液儲存池。
6.3 ?當(dāng)亞鐵充滿抽濾池后,關(guān)閉冷凍鍋放料閥。
6.4 ?打開小度水沖洗閥門,接通真空吸料,洗液在保證鈦液質(zhì)量的前提下,均勻地加入清鈦液中,剩余部分進(jìn)入小度水池。
6.5 ?用水沖洗亞鐵,回收的小度水部分返回酸解工序,剩余部分進(jìn)入小度水池,用于下批次沖洗亞鐵。
6.6 ?抽干后,停真空,通知清除吸濾池中的亞鐵。
6.7??清洗化纖地毯及清理池底亞鐵。
7、異常情況處理
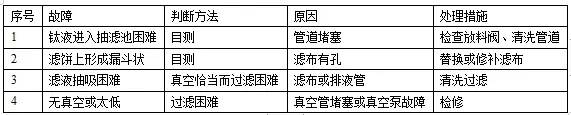
(八)?濃縮
1、目的
為了制得具有優(yōu)越顏料性能的鈦白粉,要求水解得到的偏鈦酸顆粒細(xì)而均勻,這樣對水
解所用的鈦液的濃度有一定的要求,用經(jīng)過結(jié)晶過濾的鈦液來制作是不能勝任的,因為鈦液濃度低,則水解得到的偏鈦酸的顆粒便會變粗。實踐證明,只有鈦液的TiO2含量在200g/l以上時,才能制造出具有優(yōu)越顏料性能的鈦白。為此,必須先要將鈦液進(jìn)行濃縮,使其濃度達(dá)到涂料鈦白生產(chǎn)的要求。
2、濃縮工藝流程或原理
通常情況下鈦液的沸點為104-114℃(1atm,TiO2:130-230g/l),在此溫度下長時間加熱蒸發(fā),鈦液的穩(wěn)定性會迅速下降,最終導(dǎo)致早期水解(鈦液水解的臨界溫度為80℃),這對于制造優(yōu)質(zhì)的顏料鈦白是很不適宜的。我們知道,液體的沸點是與壓力成正比的,為了降低溶液的沸點提高蒸發(fā)的效率,濃縮蒸發(fā)常常是在減壓下進(jìn)行的,稱為真空濃縮。真空度越高,溶液的沸點越低。為此,鈦液的濃縮采取真空濃縮,以降低鈦液的沸點來防止發(fā)生早期水解。為了滿足鈦液指標(biāo)、保證鈦液質(zhì)量,應(yīng)控制濃縮溫度不超過75℃,這樣真空度便不能低于0.073MPa。
3、濃縮設(shè)備
一臺30 M2濃縮器。
4、原輔動力要求
真空度????0.076MPa-0.09MPa?。
二次蒸汽溫度≤?72℃。
蒸汽壓力??0.15-0.25Mpa。
5、主要控制參數(shù)
1)質(zhì)量技術(shù)指標(biāo)
????鈦液濃度 ??193~197g/L。
2)影響濃縮產(chǎn)能的因素
(1)加料量、冷卻水量、蒸汽壓力的大小
(2)濃縮器列管的結(jié)垢情況
6、操作要點
6.1 ?首先開啟冷卻水,然后開真空泵,當(dāng)檢查冷卻水及真空度均正常后,開進(jìn)料閥,稍后開啟蒸汽加熱。
6.2 ?待濃縮開正常后,打開換熱器的進(jìn)出料閥門,啟動清鈦液送料泵。
6.3 ?開進(jìn)料閥,稍后開啟蒸汽加熱。
6.4?濃縮過程中,每小時測定一次出料玻美度,隨時注意蒸汽壓力及真空度變化情況。
6.5??濃縮停機時先關(guān)蒸汽,用少量清鈦液冷卻列管然后停真空,關(guān)冷卻水;同時停止清鈦液送料泵。
6.6??停機后排凈列管內(nèi)殘留鈦液。
7、異常情況處理
8、現(xiàn)場檢測項目
每小時檢測一次下料溫度和波美。
?
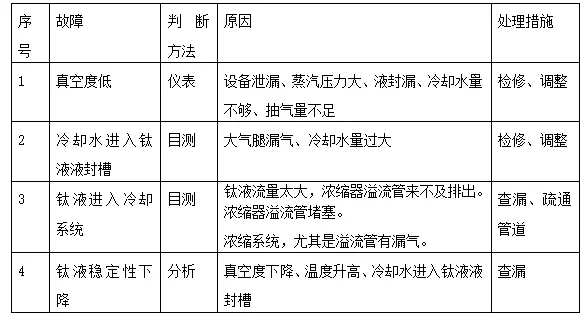
(九)?晶種
1、目的
?
2、晶種工藝流程或原理
?
3、晶種設(shè)備
φ1500×1500,Vg=m3。A3搪玻璃鋼襯2層瓷磚。
4、原輔動力要求
1)鈦液指標(biāo)
TiO2:193~197g/l ???Ti3+:1.0~3.0g/l
Fe/TiO2:0.28~0.32 ??F:1.75~1.85
穩(wěn)定性》350ml/ml ???凈化:合格
2)液堿: ??38%
?
3)蒸汽壓力》0.5Mpa
5、主要控制參數(shù)
1)質(zhì)量指標(biāo)
晶種總鈦:145 g/l ???穩(wěn)定性110~120ML ???堿濃:7.8~8.5%
2)操作條件
水解鈦液預(yù)熱溫度:96℃
3)?影響因素
?
6、操作要點
6.1 ?首先開啟冷凝水閥門,并排凈。
6.2 ?將34.8L的38%液堿與154.8L水加入晶種制備桶得到7.8~8.5 %(wt%)的液堿,并混合、攪拌5分鐘以上。 ??
6.3 ?將654L晶種鈦液在晶種預(yù)熱鍋內(nèi)用間接蒸汽在9分鐘之內(nèi)升溫至85℃,
6.4 ?將晶種預(yù)熱鍋內(nèi)堿液升溫至82~86℃(生產(chǎn)控制為85℃),用直接蒸汽加熱,升溫時間8分鐘。
6.5 ?當(dāng)堿液和晶種鈦液同時升到85℃時,?將晶種鈦液通過限流孔板在4分鐘之內(nèi)加入到晶種制備桶中,放料過程中最高溫度94.5℃,最低溫度89℃,放完料后1分鐘之內(nèi)將鈦液和堿液的混合物升到96.3℃(一般控制在94~98℃)。
6.6 ??取樣檢測晶種懸浮液穩(wěn)定性,2分鐘做完穩(wěn)定性達(dá)到100~120ml,則將晶種懸浮液放入鈦液預(yù)熱鍋,此時濃鈦液溫度為96℃。
6.7??打開鈦液預(yù)熱鍋的出口閥門, 啟動泵,向鈦液預(yù)熱鍋進(jìn)料,同時開啟攪拌。進(jìn)料達(dá)30m3時,停泵,關(guān)閉泵前后閥門。
6.8??打開預(yù)熱鍋蒸氣閥, 將鈦液加熱到96℃,并保持鈦液溫度。
6.9?將制備好的晶種鈦液放入預(yù)熱鍋,并攪拌20分鐘。
???7、異常情況處理

???8、計算
?
???9、現(xiàn)場檢測項目
每批檢測一次穩(wěn)定性。
(十)?水解
1、目的
鈦液的水解是把二氧化鈦組分從液相(鈦液)重新轉(zhuǎn)變?yōu)楣滔啵ㄆ佀幔┑倪^程,從而與母液中的可溶性雜質(zhì)分離以提取純二氧化鈦,同時獲得具有一定大小而均勻的粒子,組成恒定的、同時易于過濾與洗滌的偏鈦酸。
2、水解工藝流程或原理
硫酸氧鈦是強酸弱堿鹽,易水解。在晶種存在下,經(jīng)稀釋和沸騰生成白色偏鈦酸沉淀。
其反應(yīng)方程式如下: ?????
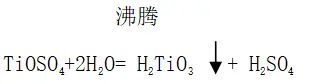
???1)第一階段----晶核的形成
???水解的第一步,是從完全澄清的溶液中析出第一批極為微小的結(jié)晶中心,稱為晶核。不同的水解條件,得到的是不同數(shù)量和具有不同組成的晶核。晶核的數(shù)量與組成決定了水解沉淀物的組成,也決定了最后成品的性質(zhì)。因此水解是二氧化鈦生產(chǎn)中最主要的一環(huán),而形成結(jié)晶中心是水解過程中最重要的一環(huán)。
???在實際生產(chǎn)中,生成晶核有二種方法,一種是在原來溶液中培養(yǎng)晶核,即所謂自生晶種;另一種是另外制造晶核,而后把它引人澄清的溶液中去,即所謂外加晶種。
???2)第二階段----晶核的成長與沉淀的形成
???當(dāng)晶核形成后,如果使水解作用繼續(xù)進(jìn)行,則根據(jù)結(jié)晶原理,在晶核表面便發(fā)生鈦的固析。這就促使晶核逐漸累積長大,當(dāng)達(dá)到相當(dāng)大小時便成為沉淀而沉析出來。
???3)第三階段----沉淀物的組成以及溶液組成,隨著水解作用的進(jìn)展而改變當(dāng)沉淀物開始析出后,水解作用仍以較大的速度在進(jìn)行,晶體繼續(xù)成長。在這階段里,溶液的成分隨著沉淀而不斷變化。TiO2的含量逐漸降低,而游離酸濃度不斷提高。這個變化直接影響了沉淀物的組成,能使沉淀的粒子局部溶解,而后又重新析出新組成的沉淀,也可能是固體沉淀物的直接轉(zhuǎn)化。這個過程不斷繼續(xù)直到水解完全,溶液中只剩下及少數(shù)的鈦及較濃的硫酸,此時沉淀物的組成才最后固定下來。
???鈦液中三價鈦離子的水解pH值接近于3,并且不具有膠體特征,所以在熱水解過程中它不發(fā)生水解反應(yīng),不產(chǎn)生沉淀。在熱水解結(jié)束后仍留在母液中。但由于攪拌及沸騰的影響,會有部分被空氣氧化而成為硫酸氧鈦。
??

???水解后母液中應(yīng)保持Ti+3含量在0.5克/升左右。
3、水解設(shè)備
φ4000×(4100+800),Vg=50m3。A3搪瓷襯2層瓷磚。
4、原輔動力要求
1)濃鈦液質(zhì)量指標(biāo)
60℃波美:?????50~52Be′????????總鈦???193-197g/L
Fe/TiO2 ?????????0.28-0.32???????Ti3+?????1-3g/L
F值????????????1.75-1.85 ???????穩(wěn)定度??≥350
凈化 ??????????合格
2)蒸氣壓力??≥0.2MPa
5、主要控制參數(shù)
??1)質(zhì)量技術(shù)指標(biāo)
水解率?????≥94.5% ??????
過濾速度???4~6Min
偏鈦酸中Ti3+≥0.8g/L
????沉降度 ????80~100mm
2)操作條件
保壓壓力 ?30~100MM水柱
木質(zhì)纖維素加入比列 ???2.4‰ ????攪拌30min
4)?影響因素
(1)鈦液的性質(zhì)和組成
????在鈦液熱水解時水解鈦液的組成和質(zhì)量對偏鈦酸的純度,微晶體的結(jié)構(gòu)和膠粒的大小影響很大。尤其在生產(chǎn)顏料鈦白時鈦液的含鈦量、F值、鐵鈦比、三價鈦含量、澄清度和穩(wěn)定性必須符合一定的要求。現(xiàn)分述如下。
????鈦液的穩(wěn)定性和澄清度
???在儲存和放置過程中,鈦液有陳化而逐漸析出膠狀渾濁或沉淀的傾向,表示這種傾向強弱的特性稱為鈦液的穩(wěn)定性。在穩(wěn)定性差的鈦液中,水解前本身已產(chǎn)生了某些膠性的結(jié)晶中,在水解時這些結(jié)晶中心便起著不良的作用,使得到的偏鈦酸粒子不均勻并且容易吸附較多的雜質(zhì),不但使偏鈦酸的洗滌時間延長,而且在煅燒時二氧化鈦的粒子容易燒結(jié),使最終產(chǎn)品的白度、著色力和分散性能都會顯著下降。
?????澄清度與穩(wěn)定性有密切關(guān)系。對穩(wěn)定性差的鈦液,在過濾凈化時靠通常的助濾層并不能提高溶液的穩(wěn)定性,因為這些可以作為結(jié)晶中心的膠粒極易透過濾層,這使澄清度也不理想。如果是因為過濾操作不當(dāng)而引起的澄清度不良,則會使鈦液含有不溶的固體懸浮雜質(zhì),即使其量很少也會較低產(chǎn)品的純度、白度和其他顏料性能。因此,必須嚴(yán)格控制水解鈦液的澄清度。
???鈦液的濃度
???水解鈦液的濃度對二氧化鈦成品的粒子和顏料性能影響極大。含鈦量較低的鈦液,例如含TiO2小于150克/升水解生成的偏鈦酸,煅燒后則轉(zhuǎn)化為粗分散型二氧化鈦,它的顏料性能極差。
????當(dāng)水解鈦液濃度較低時隨著TiO2濃度的提高,最終產(chǎn)品的著色力隨著提高。但是提高TiO2濃度會減慢水解速度,開始水解的時間也相對延長,水解率也會下降。因此對于非顏料用鈦白,因?qū)Ξa(chǎn)品并無顏料性能的要求,多采用低濃度鈦液水解以獲得較高的水解率并使偏鈦酸容易水洗。在制造顏料用的細(xì)分散型二氧化鈦時,則必須提高熱水解時的鈦液濃度至含TiO2?190--230克/升方能制得質(zhì)量合乎要求的顏料用鈦白。
???鐵鈦比
???在水解時,鈦液中硫酸亞鐵的高低,對水解反應(yīng)也有一定的影響。硫酸亞鐵的存在能增加溶液的比重和粘度,提高了總離子濃度。故提高鐵鈦比熱水解速度便減慢,水解率也會降低而得到的偏鈦酸也會越細(xì)。同時由于鐵鈦比的增加,母液的粘度和比重都會上升,這就使偏鈦酸的洗滌速度減慢。所以,在水解鈦液中鐵鈦比必須適當(dāng)。在工業(yè)生產(chǎn)中,一般控制鐵鈦比在0.2-0.3之間。過低的鐵鈦比雖然有利于偏鈦酸的洗滌,但會增加冷凍工序的負(fù)擔(dān)并使得到的偏鈦酸變粗。
????酸度系數(shù),F(xiàn)值
????在相同濃度的鈦液中,F(xiàn)值大則酸度也高,水解反應(yīng)便受到抑制,使水解速度變慢,水解率降低。在常壓水解中,F(xiàn)值越低到水解開始的時間越短,反之則到水解開始的時間越長。但F值過低,鈦液容易發(fā)生早期水解,這種鈦液水解時不但偏鈦酸粒子不規(guī)則,而且水解無法控制。因此,對顏料用鈦白,一般銳鈦型生產(chǎn)時F值控制在1.8-2.0,金紅石型生產(chǎn)時控制在1.9-2.1。
????三價鈦的濃度
????鈦液中三價鈦離子的存在能防止亞鐵氧化成二價鐵,但三價鈦過多不但影響水解率,而且三價鈦對水解還有抑制作用。所以水解前溶液中必須能保證水解后的母液中還有0.5克/升左右的三價鈦。
????鈦液中的雜質(zhì)含量
????除了硫酸亞鐵外,鈦液中存在的雜質(zhì)可分為二類,一類是溶解的可溶性磷酸鹽,另一類是不溶于硫酸的固體雜質(zhì),固體雜質(zhì)可通過過濾來除去。在溶解的雜質(zhì)中,根據(jù)原礦成分含有鋁、鉻、鎂、錳、釩、鈮、鈉或鉀的硫酸鹽和磷酸鹽,以及由于設(shè)備材質(zhì)選擇不當(dāng)在生產(chǎn)過程中腐蝕而生成的磷酸鹽。只要這些元素中某幾種進(jìn)入偏鈦酸中,即使其含量少到不能用普通化學(xué)分析方法來測定的程度也會影響最終產(chǎn)品的白度和光澤。
?????鈦液的固含量
鈦液的固含量除含有部分未被除去的固體雜質(zhì)外,還有部分鈦液早期水解的產(chǎn)物這些雜質(zhì)在水解過程中都是不良的結(jié)晶中心,會破壞水解的過程,使偏鈦酸粒度不均勻,而影響成品的質(zhì)量。
(2)水解的操作
???鈦液和底水的預(yù)熱溫度
???鈦液和底水的預(yù)熱溫度直接影響著晶種生成溫度,太高太低都會影響晶種的數(shù)量和質(zhì)量故此溫度必須在要求的范圍內(nèi),不能太高或太低。
???底水的加量
???底水加量與濃鈦液的比值決定著晶種的數(shù)量,底水量過多則會造成晶種數(shù)量太多,反之底水量過少則晶種數(shù)量不足,從而影響水解率和偏鈦酸的粒徑,造成對成品質(zhì)量的影響。
???變灰點的控制
???變灰點的判斷應(yīng)為水解誘導(dǎo)期結(jié)束,水解反應(yīng)快速進(jìn)行時最好,太早太遲都會導(dǎo)致水解反應(yīng)速度不理想而影響產(chǎn)品的粒度分布,影響成品質(zhì)量。
????升溫速度
????升溫時間的控制同樣影響水解反應(yīng)速度,從而影響最終成品的質(zhì)量。
????沸騰程度
沸騰程度的大小,跟供給的熱量有關(guān),沸騰程度太小,供給的熱量就不足,從而影響偏鈦酸的水解速度,使偏鈦酸的水解率偏低。如果沸騰太過劇烈,會破壞偏鈦酸的絮凝,故應(yīng)使料液保持微沸騰為好。
6、操作要點
6.1??打開預(yù)熱鍋的放料閥,將混合好的鈦液放入水解鍋中,并開啟攪拌。
6.2??放料3分鐘后開大汽閥。
6.3 ?放完料約13分鐘,在15分鐘內(nèi)用直接蒸汽升溫至溶液沸騰,沸點約103-108℃。
6.4 ?大沸3分鐘后,停汽、開攪拌30分鐘。
6.5 ?再次升溫至溶液沸騰。升溫前,溶液溫度降低至105℃,20分鐘內(nèi),將溶液升溫至沸騰,第二沸點為105-109℃。
6.6??達(dá)到第二沸點以后,馬上關(guān)閉主蒸汽閥,開啟自動保壓閥,壓力控制在30~100mmH保
壓時,關(guān)閉水解鍋鍋蓋以及排煙囪,當(dāng)壓力超過規(guī)定范圍時,自動停止加熱蒸汽。
6.7??保壓180分鐘后,完成水解。保壓期間,溶液最高溫度為112℃。
6.8??向水解鍋加入16.6公斤木質(zhì)纖維素,攪拌30分鐘。
6.9??取樣,放料約30分鐘。
6.10啟動石墨冷卻器的冷卻水泵,打開石墨冷卻器的冷卻水進(jìn)出閥門,再打開水解鍋放料閥, 將料放入偏鈦酸貯存桶,并保持漿料溫度60~70℃。
6.11洗鍋,約15~30分鐘。
6.12啟動給料泵,向水洗吸片池送料。
7、異常情況處理
?
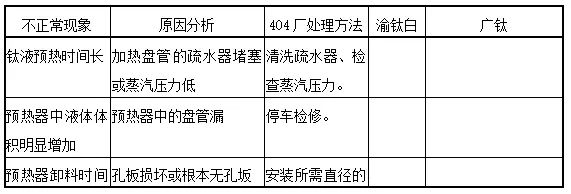
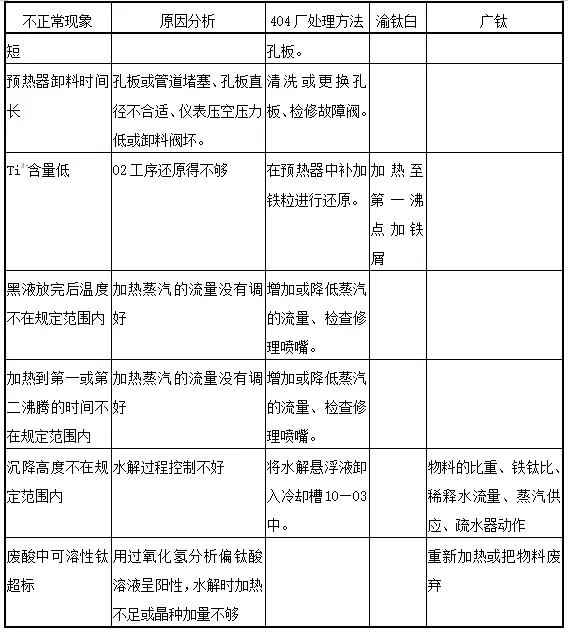
(十一)?一洗
1、目的
熱水解得到的偏鈦酸懸浮液是一種具有粒狀結(jié)構(gòu)的凝膠,在放置過程中會緩慢沉淀下來,偏鈦酸顆粒吸附著大量母液,母液成分主要是游離硫酸和硫酸亞鐵等可溶性雜質(zhì),并含有鐵、鉻、釩、銅、錳等氧化物的雜質(zhì)離子。水洗的主要目的是除去可溶性雜質(zhì)。
2、水洗工藝流程或原理
水洗主要是利用偏鈦酸的水不溶性和雜質(zhì)離子的水溶性進(jìn)行液固分離。
3、水洗設(shè)備
M=100m2,
4、原輔動力要求
吸片真空度?≥0.065MPa ?洗水溫度40-60℃???????HF濃度???3-5%
漿料溫度???60-70℃?????漿料濃度???175-180g/l
5、主要控制參數(shù)
1)操作條件
??濾餅厚度35-40mm ??????????鏟片前抽干時間 5min
洗滌時間???2.0-3.0hr??????上完片抽干時間 5min ??
2)質(zhì)量技術(shù)指標(biāo)
游離酸濃度:≤50g/l。
漿料濃度:300~400?g/l。
3)影響因素
(1)真空度的影響
????過濾介質(zhì)兩側(cè)的壓力差就是真空度。在真空管線不漏氣的條件下,過濾的真空度除了真空泵的能力外是濾餅和過濾介質(zhì)的阻力來決定的,水合二氧化鈦的過濾一般以67千帕(500毫米汞柱)以上的真空度較為合適。真空度過低,水洗時間就長,而且容易產(chǎn)生落片事故。
(2)水合二氧化鈦顆粒度的影響
????過濾要求固體顆粒均勻而適中。顆粒粗、水流快,便容易洗滌,但顆粒過粗,會使水流速度過快而增加管道阻力,粒子內(nèi)部也不易洗凈。顆粒過細(xì)會堵塞濾布孔眼,降低水流速度,影響產(chǎn)量,穿濾現(xiàn)象也較嚴(yán)重。
(3)水的溫度的影響
????水洗過程主要是除去硫酸亞鐵及游離硫酸,硫酸亞鐵在水中的溶解度在一定溫度范圍內(nèi),隨著溫度的升高而增大。因此提高水溫有利于水洗,可以縮短時間,降低含鐵量,減少用水量,提高產(chǎn)量。從硫酸亞鐵在水中的溶解度曲線圖中可以看出在60℃時硫酸亞鐵的溶解度最大,但超過45℃時朔料容易變形,因此水溫一般控制在30-40℃,溫度過低時,甚至在濾餅內(nèi)也會有硫酸亞鐵細(xì)粒結(jié)晶析出,水洗效果大大下降。
(4)酸度的影響
????隨著水洗過程的進(jìn)行,濾餅內(nèi)的酸度逐漸降低,pH值相應(yīng)升高,同時由于溶于水中的氧可使部分亞鐵離子氧化成高鐵離子,當(dāng)pH值高于2.5時,它會水解而沉淀出不溶于水的氫氧化高鐵或生成難溶于水的堿式硫酸鐵;當(dāng)pH值升到4以上時,硫酸亞鐵也可能水解而沉淀。因此在酸度較高階段盡快除鐵是水洗的關(guān)鍵,提高酸度有助于抑止鐵鹽水解,對水洗有利。因此如果在洗滌水中配以少量硫酸或鹽酸,使pH值始終保持在1-2左右,可防止鐵鹽水解而保持可溶狀態(tài),水洗后偏鈦酸含鐵量可降低到能與漂洗相媲美的程度。
(5)水質(zhì)的影響
水質(zhì)對水洗效果影響較大,水中雜質(zhì)主要有鈣、鎂(硬水)、鐵等離子,江河水和深井水的鈣、鎂離子含量較高,水洗時鈣離子與硫酸根形成不溶的硫酸鈣沉淀混入產(chǎn)品而影響質(zhì)量。水中含鐵量較低,但用鐵鹽作凝聚劑時,鐵含量就偏高。
(6)時間的影響
偏鈦酸開始水洗時,物料酸度高,雜質(zhì)濃度梯度大,洗滌效率較高。開始水洗時,偏鈦酸中含鐵時迅速降低,半小時內(nèi)可除去80%以上,隨著水洗過程繼續(xù)進(jìn)行,雜質(zhì)在濾餅與濾液間的濃度梯度逐漸減小,酸度也逐漸下降,同時由于離子濃度不斷降低,偏鈦酸的膠體性質(zhì)逐漸明顯,水洗效率隨之降低。通常偏鈦酸的洗滌時間是抽濾時間的150-200%,再延長洗滌時間,不僅無益,而且有害。因此水洗過程僅能使含鐵量降低至一定程度,殘留的鐵需在漂洗過程中進(jìn)一步除去。
(7)三價鈦鹽的影響
濾餅內(nèi)存在三價鈦離子,可防止出現(xiàn)高鐵離子,因此水洗過程中保持一定量三價鈦離子對水洗是有利的。實踐表明,漿液中三價鈦含量較高,水洗時間相應(yīng)縮短,水洗后偏鈦酸略帶灰相,含鐵量也較低,煅燒后成品色澤較白,這一點對常壓水解產(chǎn)品更為明顯。
(8)過濾介質(zhì)的影響
漿料過濾時,使固液分離的隔離物質(zhì)稱為過濾介質(zhì),真空葉濾機的過濾介質(zhì)是濾布。因漿液酸度很高,過濾介質(zhì)必須是耐酸材料。曾提出用尼龍布、多孔橡膠、硝化纖維布、維綸布、滌淪布、玻璃布等等,國內(nèi)常用758#滌淪布。濾布孔度對水洗效率直接有關(guān),孔眼過細(xì)容易被物料堵塞,孔眼過大容易造成物料穿濾。758#為短纖維滌淪布,過濾速度快,但容易發(fā)生落片現(xiàn)象,特別是調(diào)換新布后更易落片,因此一般采用絮凝劑或助濾層。
6、操作要點
6.1 ?將沖洗干凈的葉濾機吊入濃漿池中,浸沒葉片,打開真空閥開始吸片,控制厚度35-40mm。
6.2 ?用行車將葉濾機吊到水洗池中洗滌,水洗過程中,要調(diào)好進(jìn)出水量始終保持水浸沒葉片。
6.3 ?水洗合格的葉片吊至鏟片池上方,抽干后斷真空,鏟片。
6.4 ?在打漿桶中加水調(diào)好漿料濃度,將漿料打漿混合,用泵定量打入漂白鍋。
6.5 ?進(jìn)入低位槽的廢酸要進(jìn)行回收。
7、異常情況處理

8、計算
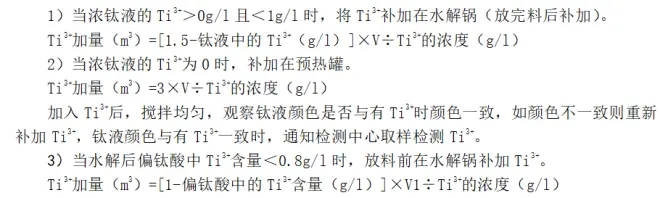
V―――水解鍋的鈦液體積M3
V1―――水解后偏鈦酸的體積M3
9、現(xiàn)場檢測項目
每批檢查洗滌時間。
?
(十二)?漂白
1、目的
經(jīng)過水洗的偏鈦酸中存在有痕量的鐵、銅、鉻、釩等雜質(zhì)。在生產(chǎn)涂料用鈦白粉時,這些雜質(zhì)將嚴(yán)重影響鈦白的白度。這種影響及其程度可由表中看出。 ???????
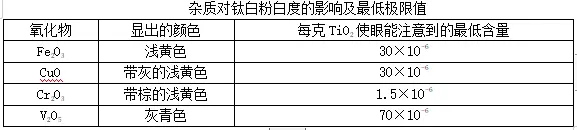
2、漂白工藝流程或原理
經(jīng)水洗的偏鈦酸中的鐵雜質(zhì)是以三價鐵離子水解生成的極為細(xì)小的固體氫氧化高鐵的形式存在的。漂白就是先將固體氫氧化高鐵轉(zhuǎn)化為可溶性的硫酸鹽,然后用化學(xué)活潑性強的金屬或金屬離子將其還原為低價的硫酸鹽,最終通過水洗進(jìn)一步除去。發(fā)生的化學(xué)反應(yīng)是氫氧化高鐵溶轉(zhuǎn)化為硫酸高鐵,硫酸高鐵在還原劑的作用下被還原成硫酸亞鐵。
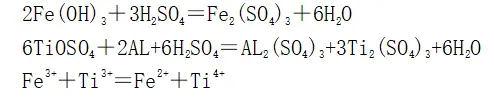
3、漂白設(shè)備
φ2600×3200,Vg=16m3。涂塑。
4、原輔動力要求
1)來料漿料濃度: 300-400g/l
2)蒸汽壓力: ?0.5-0.7Mpa
3)鋁粉 ?外觀:灰色粉末。
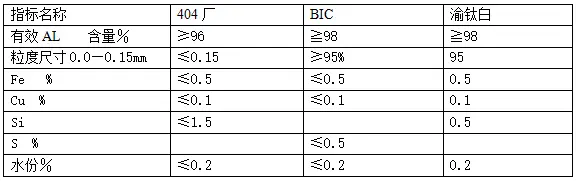
4)來料鈦液指標(biāo): 清鈦液指標(biāo)
5、主要控制參數(shù)
1)質(zhì)量技術(shù)指標(biāo)
Ti3+還原率:≥95%。
漿液中Ti3+含量:0.7-1.0g/l。
2)操作條件
漂白硫酸濃度: 25 g/l
攪拌轉(zhuǎn)速: ?60r/min
保溫溫度: ?60℃
保溫時間: ?1h
混合時間: ?30min
加入木質(zhì)纖維素攪拌時間:30?min ???加入量:2.4‰
晶種加量:≤6% ??攪拌時間:30?min
6、操作要點
6.1 三價鈦制備
6.2 檢查三價鈦鍋是否放空、干凈。
6.3 加入清鈦液0.3m3,取樣分析總鈦和F值。
6.4 啟動攪拌根據(jù)鈦液指標(biāo)加水稀釋到濃度70g/l。
6.5 ?加入計量的硫酸?????????????????
6.6 升溫到70℃后加入計量的鋁粉。
6.7 升溫到80℃保溫2h結(jié)束,停攪拌。通知化驗室取樣分析溶液三價鈦含量。
6.8 漂白
6.9 ?在漂白鍋內(nèi)加入12m3偏鈦酸,開啟攪拌。
6.10 ?加入計算的硫酸量。
6.11 ?加入計量的三價鈦混合。
6.12 ?開蒸汽升溫到60℃。
6.13 ?保溫1小時停攪拌,取樣分析漿液Ti3+含量。若Ti3+低于0.7g/l,補加三價鈦溶液,再攪拌保溫直至合格為止。
6.14 三價鈦合格后加入計量的金紅石晶種及木質(zhì)纖維素,并攪拌30 min。
7、異常情況處理

8、計算
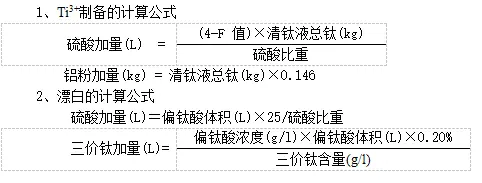
?
(十三)?二洗
1、目的
在一洗的基礎(chǔ)上進(jìn)一步降低雜質(zhì)的含量,滿足顏料鈦白的要求。
2、二洗工藝流程或原理
同一洗。
3、二洗設(shè)備
同一洗
4、原輔動力要求
吸片真空度?≥0.04MPa ?????洗水溫度50-60℃
漿料溫度???≥45-60℃ ?????來料濃度 ??350±50g/l
5、主要控制參數(shù)
1)操作條件
???HF濃度 3-5%????????????上完片抽干時間 5min
???濾餅厚度 35-40mm????????鏟片前抽干時間 5min ?
2)質(zhì)量技術(shù)指標(biāo)
Fe含量≤ 100ppm。
漿料濃度:300~340 g/l
6、操作要點
6.1 ?將沖洗干凈的葉濾機吊入濃漿池中,浸沒葉片,打開真空閥開始吸片,控制厚度35-40mm。
6.2 ?用行車將葉濾機吊到水洗池中洗滌,水洗過程中,要調(diào)好進(jìn)出水量始終保持水浸沒葉片。
6.3 ?洗滌2小時后,要經(jīng)常測定洗滌水含鐵量。
6.4 ?漂洗合格的葉片吊至鏟片池上方,抽干后斷真空,鏟片。
6.5 ?在打漿桶中加水調(diào)好漿料濃度,將漿料打漿混合后,用泵定量打入偏鈦酸貯存桶。
6.6 ?進(jìn)入低位槽的廢酸要進(jìn)行回收。
7、異常情況處理
同一洗。
8、現(xiàn)場檢測項目
檢查洗滌效果。
?
(十四)?窯前脫水
1、目的
保證進(jìn)轉(zhuǎn)窯的偏鈦酸的水份含量滿足工藝要求。
2、窯前脫水工藝流程或原理
?
3、窯前脫水設(shè)備設(shè)備
M=80m2兩臺。
4、原輔動力要求
偏鈦酸鐵含量?????????≤50ppm
過濾前偏鈦酸固含量???320g/l
????壓空壓力 ????????????0.12~0.18?Mpa
5、主要控制參數(shù)
1)質(zhì)量技術(shù)指標(biāo)
過濾后偏鈦酸濃度?????≥45%
2)操作條件
進(jìn)料壓力?????????????<1.6 Mpa??????濾布型號 ????????????3927#
濾餅厚度 ????????????30MM
6、操作要點
6.1 ?合上空氣開關(guān),按下前進(jìn)按鈕,壓緊板開始壓緊,壓力達(dá)到電接點壓力表的上限時,電機自動停止運轉(zhuǎn)。
6.2 ?打開所有出液閥門,關(guān)閉水洗、吹氣閥門。
6.3 ?打開進(jìn)料閥門四分之一,啟動進(jìn)料泵,開始進(jìn)料,此時壓濾機處于自動保壓狀態(tài),在壓力的作用下,濾漿經(jīng)過濾介質(zhì)(濾布)開始過濾,當(dāng)壓力達(dá)到電接點壓力表的下線時,壓濾機會自動補壓。
6.4 ?觀察濾液及進(jìn)料壓力變化情況,如壓力超高,需打開回流管上的閥門進(jìn)行調(diào)節(jié)。
6.5 ?由于濾布的毛細(xì)現(xiàn)象,剛開始過濾時,濾液有少許渾濁,一般明流機型5~10分鐘(暗流機型10~20分鐘)后,可將進(jìn)料閥開大,進(jìn)料時間約5~7分鐘,進(jìn)料壓力0.52 Mpa。
6.6 ?停止進(jìn)料泵,關(guān)閉進(jìn)料閥。
6.7 ?打開吹氣閥,吹3~5分鐘之后關(guān)閉吹氣閥。
6.8 ?按下“后退”按鈕,電磁球閥得電,進(jìn)行卸壓,延時15秒鐘后壓緊板自動后退,與行程開關(guān)
接觸后,電機自動停止。
6.9 ?用手動拉板器拉開濾板,人工卸料。
6.10 卸料完畢,及時清理濾板上得雜物。
7、異常情況處理
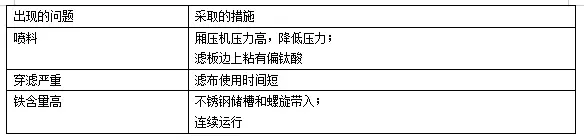
?
(十五)?鹽處理
1、目的
生產(chǎn)銳鈦型顏料鈦白粉鹽處理的目的一是使產(chǎn)品具有優(yōu)良的顏料性能;二、使銳鈦晶型起穩(wěn)定作用,抑制形成金紅石晶型,防止產(chǎn)品中混有金紅石晶型。
2、鹽處理工藝流程或原理
加入鉀鹽的作用:降低煅燒溫度、產(chǎn)品潔白、疏松、促進(jìn)二氧化鈦粒子成長。鉀鹽的添加量一般為TiO2的0.4%-2.0%,相當(dāng)于0.25%-1.4%的K2O。
加入磷酸的作用:掩蔽鐵的顏色、促進(jìn)銳鈦型的轉(zhuǎn)化、調(diào)整粒子的形狀,但會降低消色力和提高脫硫溫度。
3、鹽處理設(shè)備
4、原輔動力要求
1)磷酸 ?為無色無臭粘稠液體,應(yīng)選用試劑級。
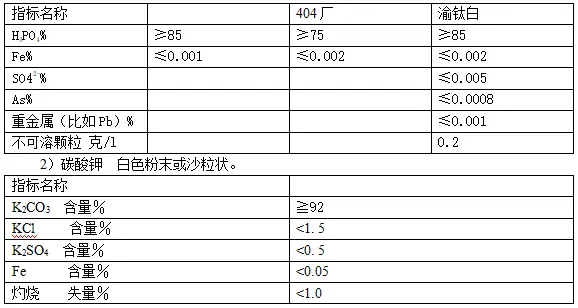
6、計算
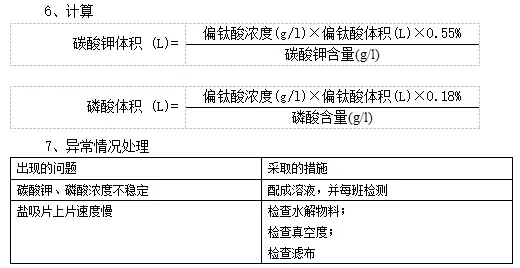
???
?
(十六)?煅燒
1、目的
煅燒過程主要是除去偏鈦酸中的水份和三氧化硫,同時使二氧化鈦轉(zhuǎn)變成所需要的晶型,并呈現(xiàn)出鈦白的基本顏料性能。
2、煅燒工藝流程或原理
在高溫條件下,偏鈦酸經(jīng)脫水、脫硫、粒子成長生成銳鈦型二氧化鈦,其反應(yīng)方程式如下:
? ?
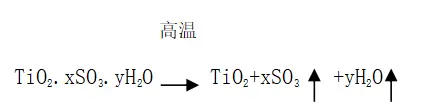
3、煅燒設(shè)備
φ2500×45000
4、原輔動力要
煤氣熱值≥
5、主要控制參數(shù)
外觀 ????白色軟體粉沫 ??????????消色力 ??90~100 ?
白度 ????≥微差于 ??????????????PH值 ????6.5-8.5 ?
6、操作要點
1)首先,送給煅燒脫水過濾器的物料量要穩(wěn)定,每隔12小時送料速度最多允許發(fā)生一次變化,而且每一次變化不能超過5%,如果必須變動則二次每隔12小時5%的變化較每24小時發(fā)生一次10%的變化更優(yōu)越,這就是管理人員必須特別注意煅燒前的物料儲量,至少要清楚8個小時內(nèi)的儲量變化情況,管理人員還必須注意煅燒工序之前計劃的或偶然發(fā)生的生產(chǎn)變化情況,這樣,管理人員就能預(yù)測到窯加料量的變化,從而進(jìn)行如前所述的穩(wěn)定操作。
當(dāng)物料短缺、煅燒窯的送料率小于每天6噸時,就應(yīng)該停止加料并封窯。封窯包括關(guān)閉油槍、關(guān)閉排風(fēng)調(diào)節(jié)閥及燃燒室進(jìn)風(fēng)口,其意圖是盡量保持窯內(nèi)的熱量。封窯后,每15分鐘應(yīng)把窯轉(zhuǎn)動半周一避免筒體變形。
2)如前所述,操作者必須根據(jù)要求調(diào)節(jié)燃燒室的溫度和排風(fēng)機調(diào)節(jié)閥的開度,調(diào)節(jié)的程度和調(diào)節(jié)的時間由富有操作經(jīng)驗的人員來判斷。溫度和風(fēng)量的調(diào)節(jié)沒有硬性和有速效的規(guī)定,但下述內(nèi)容可以作為指導(dǎo):
一旦做出一次調(diào)節(jié)后,應(yīng)在第一次調(diào)節(jié)出現(xiàn)明顯效應(yīng)時再來采取第二次調(diào)節(jié)措施。按照上述指導(dǎo),就可以減少調(diào)節(jié)過度的風(fēng)險。
應(yīng)該盡量減少調(diào)節(jié)次數(shù),并使調(diào)節(jié)范圍越小越好。然而,進(jìn)行一次有效的調(diào)節(jié)一個小時內(nèi)不需進(jìn)行再度調(diào)節(jié)總比頻繁的數(shù)次小調(diào)節(jié)要好,采用這種方法操作者能使煅燒窯保持在控制條件中。
如果溫度突然變化,首先查找原因。比如,如果發(fā)現(xiàn)脫水過濾器的送料中斷15分鐘,那么在這種情況下最好不要調(diào)節(jié),“順其自然”。最好的辦法是“如有疑點,別去管他”。
3)富有經(jīng)驗的煅燒操作者,其判斷能力和經(jīng)驗是通過訓(xùn)練和多年操作積累的。煅燒工序的操作主要依靠經(jīng)驗,選擇煅燒的操作人員要根據(jù)其判斷能力,一經(jīng)培訓(xùn)后就應(yīng)留在本崗位工作,而不應(yīng)再轉(zhuǎn)到別的崗位。白班管理人員應(yīng)盡可能隨時地與煅燒班長討論煅燒操作條件的變化情況,但絕不能超越班長和操作者隨時去操作。
4)置于煙室內(nèi)的熱電偶測定從煅燒窯排出的氣體溫度。這個溫度值一般都在430~450℃內(nèi)。該溫度的上限值受氣體導(dǎo)管的材質(zhì)和氣體洗滌器能力(可以把氣體冷卻至65℃)的制約。
由于窯內(nèi)前半部分大量的濕物料,因此調(diào)節(jié)顏料最高溫度和溫度梯度,對煙箱溫度的影響很小。然而,煙箱溫度對于窯加料量的突然變化卻非常敏感,只要煙箱溫度發(fā)生劇烈變化,就應(yīng)迅速檢查窯的加料速度并予以調(diào)整。
決定最佳最大的顏料溫度和最佳溫度梯度,從而生產(chǎn)高質(zhì)量的銳鈦顏料之方法。
首先,必須強調(diào),無論煅燒操作多穩(wěn)定,但無法補救在煅燒前出現(xiàn)任何錯誤或缺陷(當(dāng)然,煅燒不佳的話也會損害顏料質(zhì)量),有四點值得注意:
很明顯,首先注意每一個工藝步驟的細(xì)節(jié),從鈦礦開始。
有時會出現(xiàn)這種情況:煅燒窯似乎運轉(zhuǎn)良好,但顏料質(zhì)量卻突然下降。在查原因時,就有必要檢查煅燒之前的各工藝步驟,同時也要檢查煅燒本身,待查出原因后,解決問題。
有時,導(dǎo)致顏料質(zhì)量下降只是暫時的,這不需要采取措施。在這種情況下,窯繼續(xù)在正常溫度下運轉(zhuǎn)直至不良品從窯排出。其后仍可以用標(biāo)準(zhǔn)來決定最佳最大的顏料溫度等工藝操作條件。比如,一個操作者可以生產(chǎn)出一批不合格的水解物料,由于在燃燒工藝和水解工序之間的物料混合,該批不合格物料會連續(xù)幾天污染產(chǎn)品,而這種情況在窯內(nèi)無法挽回。
顏料質(zhì)量下降的快慢,可作為一種判斷原因的線索:質(zhì)量的突然下降可能是煅燒本身所致或前面幾個與煅燒緊接的步驟所致。比如,硫酸鉀或磷酸的添加量不當(dāng)、水解或鐵鈦比比列不當(dāng)。通常,質(zhì)量緩慢下降意味著質(zhì)量回升緩慢,一旦找出原因就應(yīng)迅速解決。
應(yīng)根據(jù)多次分析結(jié)果來決定是否改變最大顏料溫度或溫度梯度,取冷卻窯的物料樣品進(jìn)
行這些分析。分析頻率涉及到是否能正常操作,很顯然,如果任何一個特性指數(shù)低于相應(yīng)的標(biāo)準(zhǔn),那么針對這個特性指數(shù)的分析次數(shù)將相應(yīng)地增加直到操作條件(包括煅燒溫度)被重新確定。
7、異常情況處理
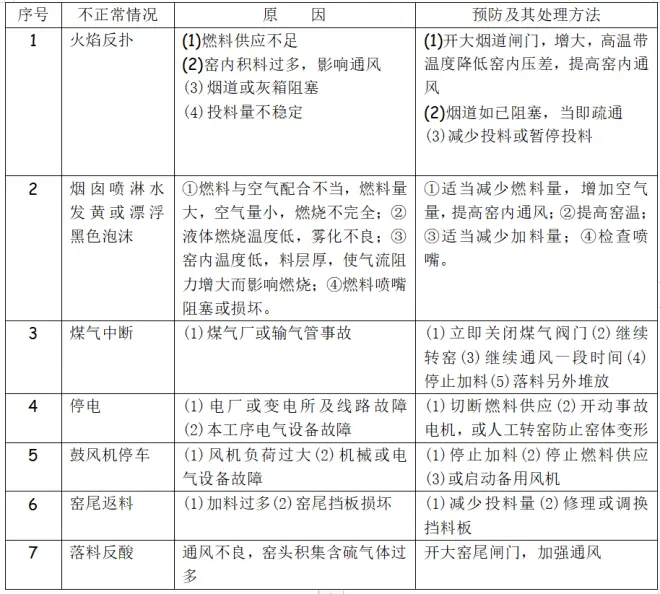
8、計算
t=0.19L/NDS
其中: t 停留時間(分鐘)
L 煅燒窯長度(英尺)
N 煅燒窯轉(zhuǎn)速 (r/min)
D 煅燒窯直徑(英尺)
S 煅燒窯傾斜度(英尺/英尺
9、現(xiàn)場檢測項目
每小時檢測一次PH值。
?
(十七)?粉碎
1、目的
通過粉碎過程使煅燒物料獲得具有一定顆粒分布的顏料鈦白。
2、粉碎工藝流程或原理
同前粉碎。
3、粉碎設(shè)備
4R3臺、5R2臺。
4、原輔動力要求
工作電壓 380V
5、主要控制參數(shù)
1)操作條件
主機電流 40~60A???????????????分級器轉(zhuǎn)速 800r/min
風(fēng)機電流 45~50A
2)質(zhì)量技術(shù)指標(biāo)
+325目≤0.02%
6、操作要點
6.1 ?啟動分級器,將轉(zhuǎn)速逐步調(diào)至能適應(yīng)成品細(xì)度的要求。
6.2 ?啟動風(fēng)機,侍正常。
6.3 ?啟動主電機,下沉后均勻加料。
6.4 ?停機時先停加料,主機再運行2-3分鐘,然后停主機、風(fēng)機及分級器。
7、異常情況處理
同前粉碎。
8、現(xiàn)場檢測項目
每小時檢測一次細(xì)度。